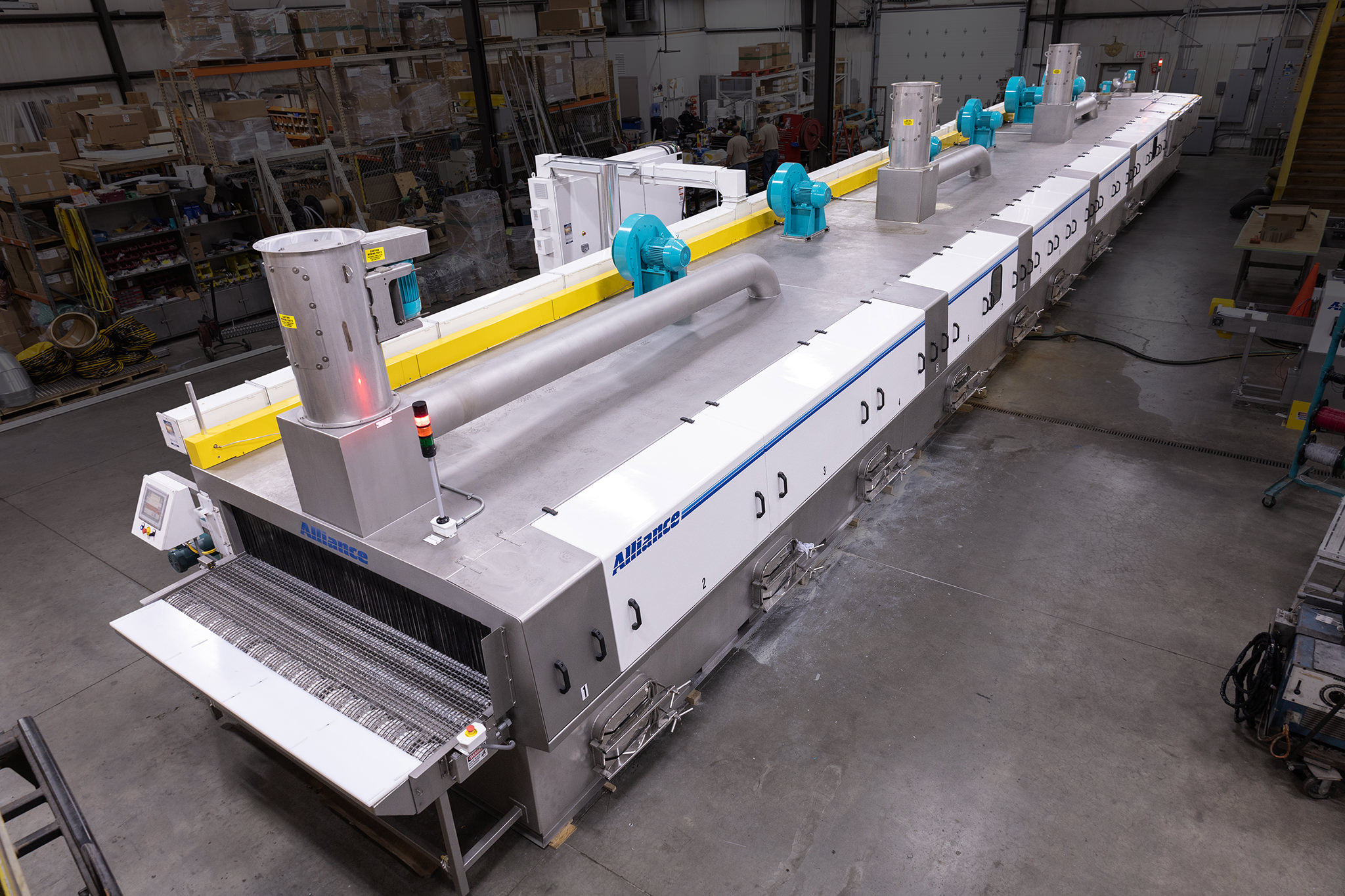
Customer Background
The customer is a major US-based manufacturer of household cookware, bakeware, kitchenware, microwave, outdoor cookware, and other consumer/restaurant products. The company sources most materials domestically, and focuses on sustainability in their manufacturing processes.
Challenge
The cookware manufacturing customer needed a cleaning system to wash, acid etch, rinse, and fully dry a variety of sizes of steel, stainless steel, and aluminum cookware and bakeware ranging from 7″ to 15″ in diameter, and 3″ to 12″ high. A high production output was required.
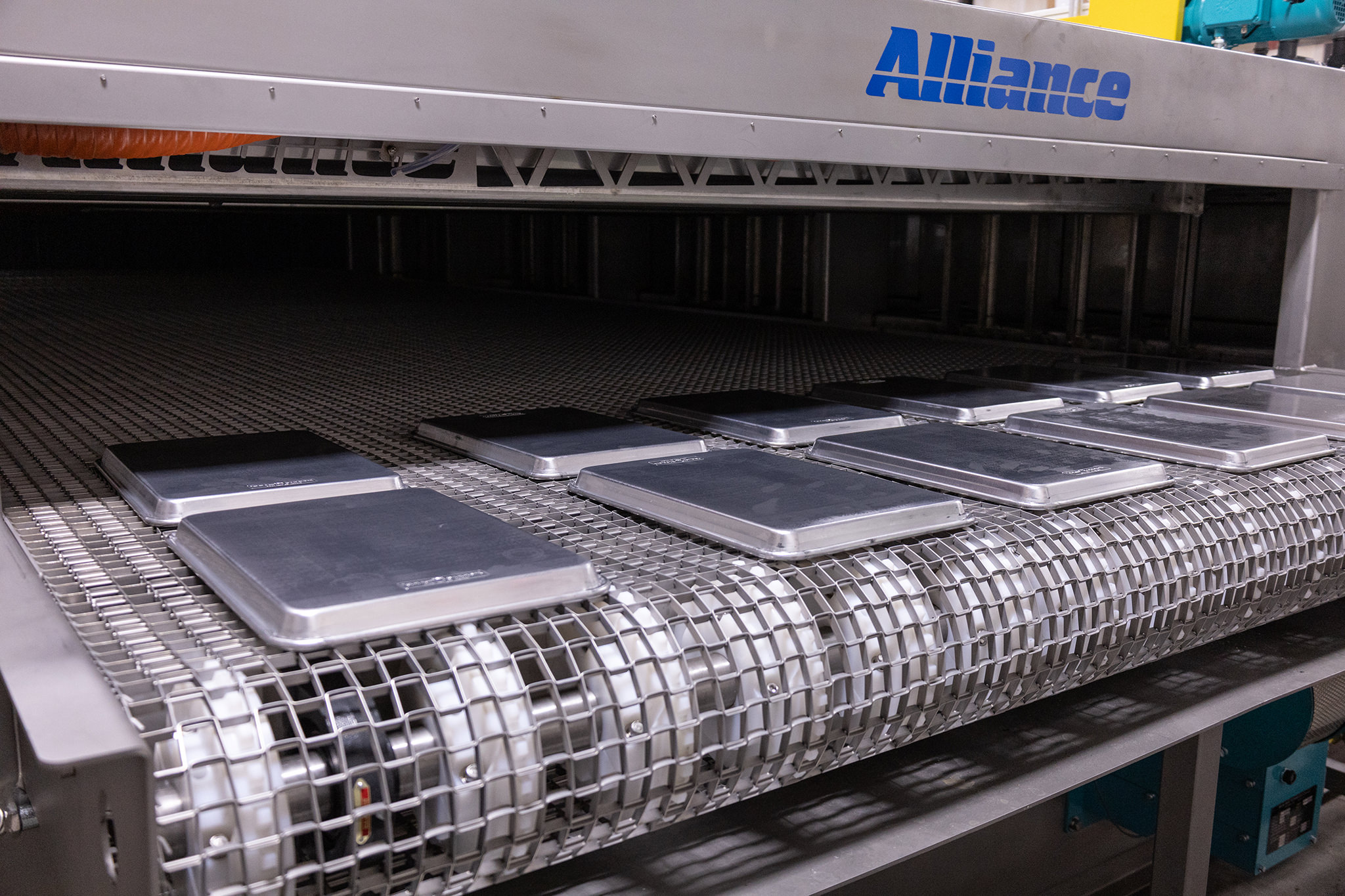
Solution
Alliance engineered a large, 80-foot long automated aqueous parts washer to meet the high production demands of the customer. The 96″ wide conveyor belt was used to handle the various sizes and amounts of the products through multiple wash, rinse, and drying stages. An acid etch stage was included to prepare the surface for a coating operation. The air knives can be set for various product heights using the operator control interface and a pneumatic lift which raises and lowers all air knives simultaneously. The spray headers, curtains, and conveyor brushes can be pulled out of the machine for easy cleaning, maintenance, and replacement. In addition, variable-frequency drive motors were used with all pumps and blowers for maximum efficiency. There is an automatic chemical injection system for the solution stages. This cookware cleaning machine utilizes gas heat and is able to heat up to 350°F in the heated blow-off zone for maximum dryness.
Cleaning Method
Aqueous cleaning was chosen for this cookware manufacturing application due to the large size and volume of products to be cleaned.
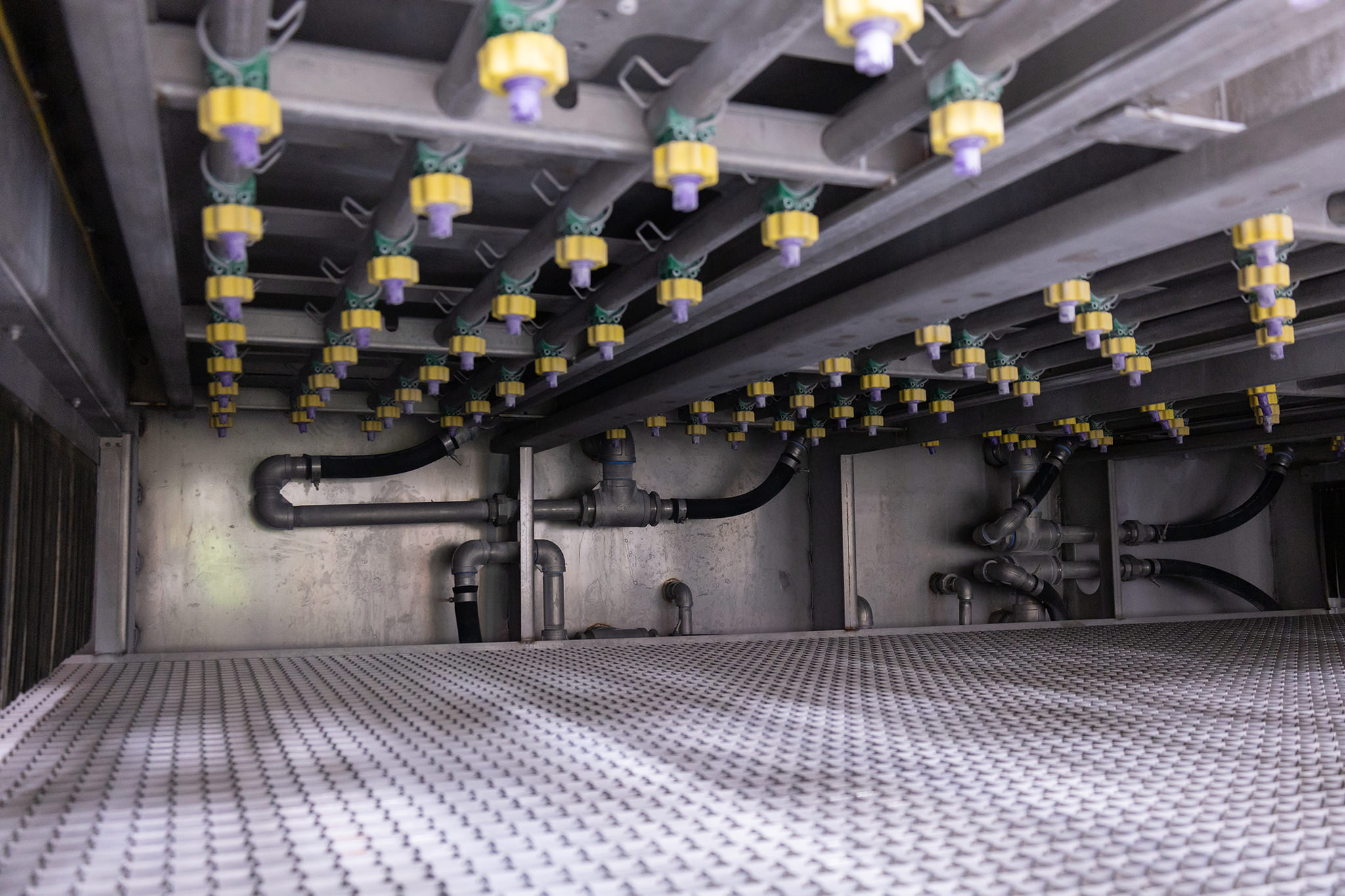
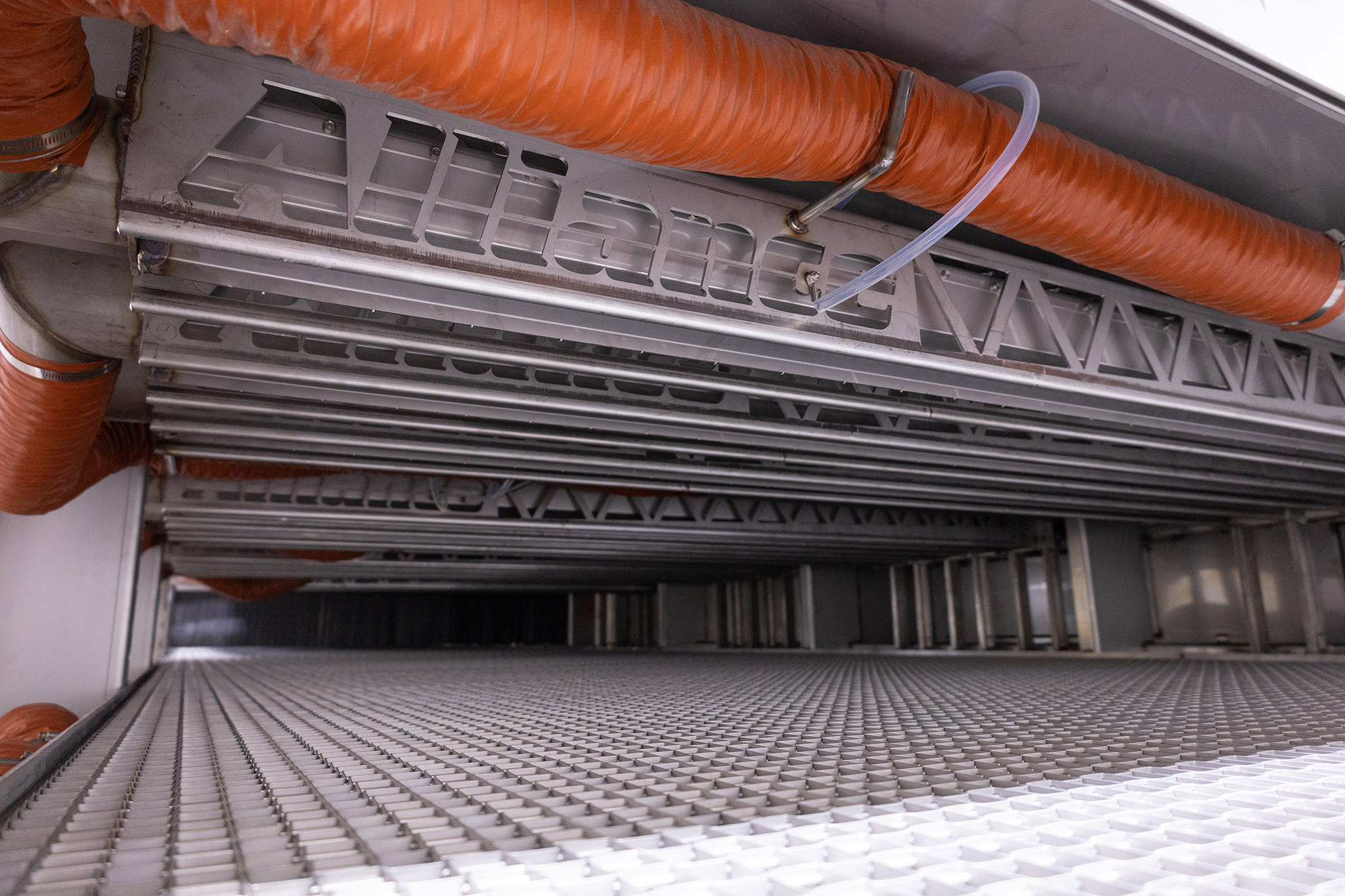