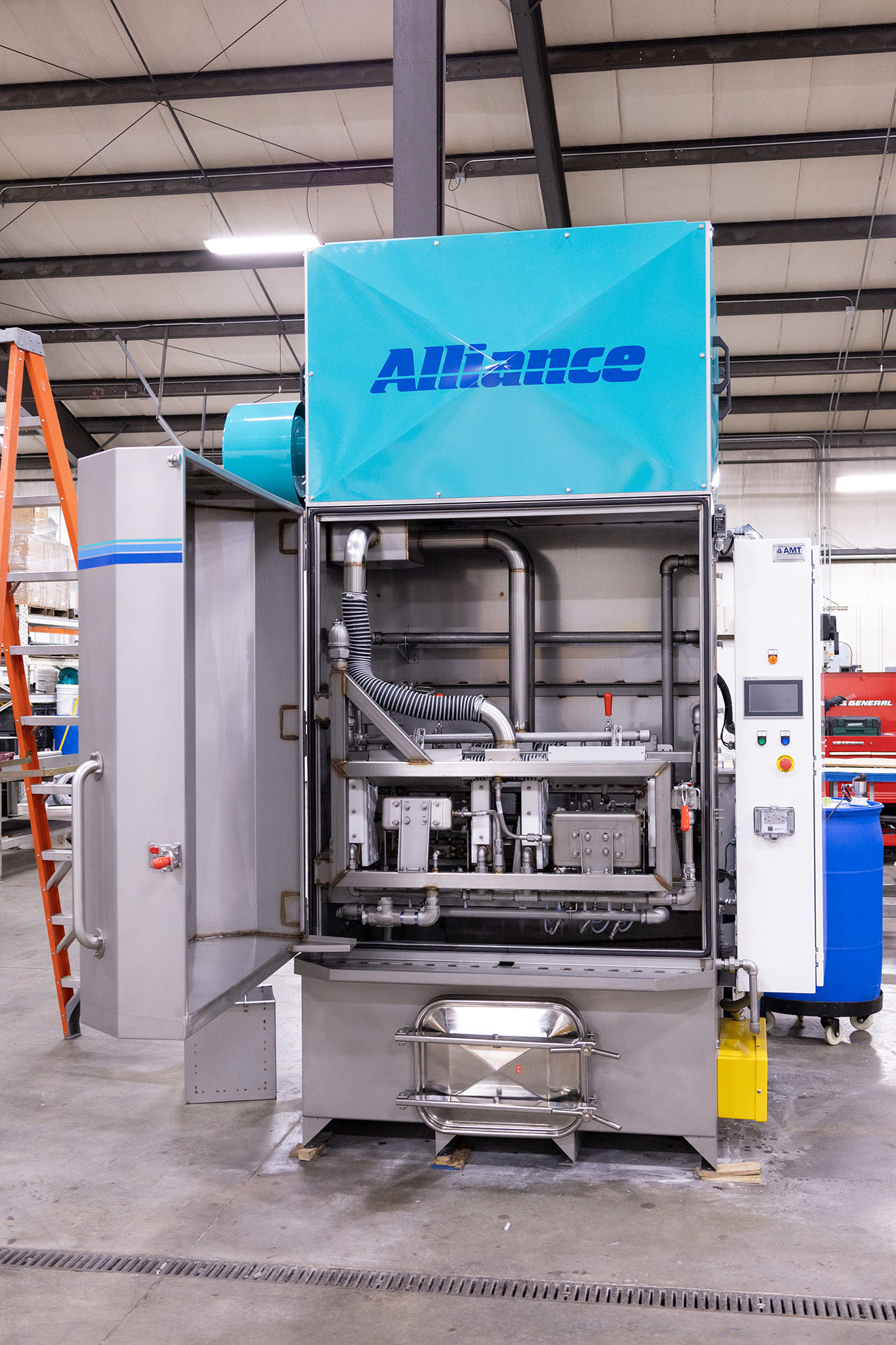
Customer Background
The customer is a leading manufacturer and supplier of powered outdoor recreational vehicles. Their lineup includes UTVs, ATVs, snowmobiles, snow sleds, pontoon boats, cruising boats, and motorcycles.
Challenge
The customer needed to remove coolant and chips from the upper and lower halves of an aluminum crankcase assembly parts. Each part style was unique, yet needed to be washed within the same cleaning cycle. The parts had many critical surfaces and blind holes and meeting a strict cleanliness specification was required. The crankcase parts needed to exit with gross amounts of moisture removed.
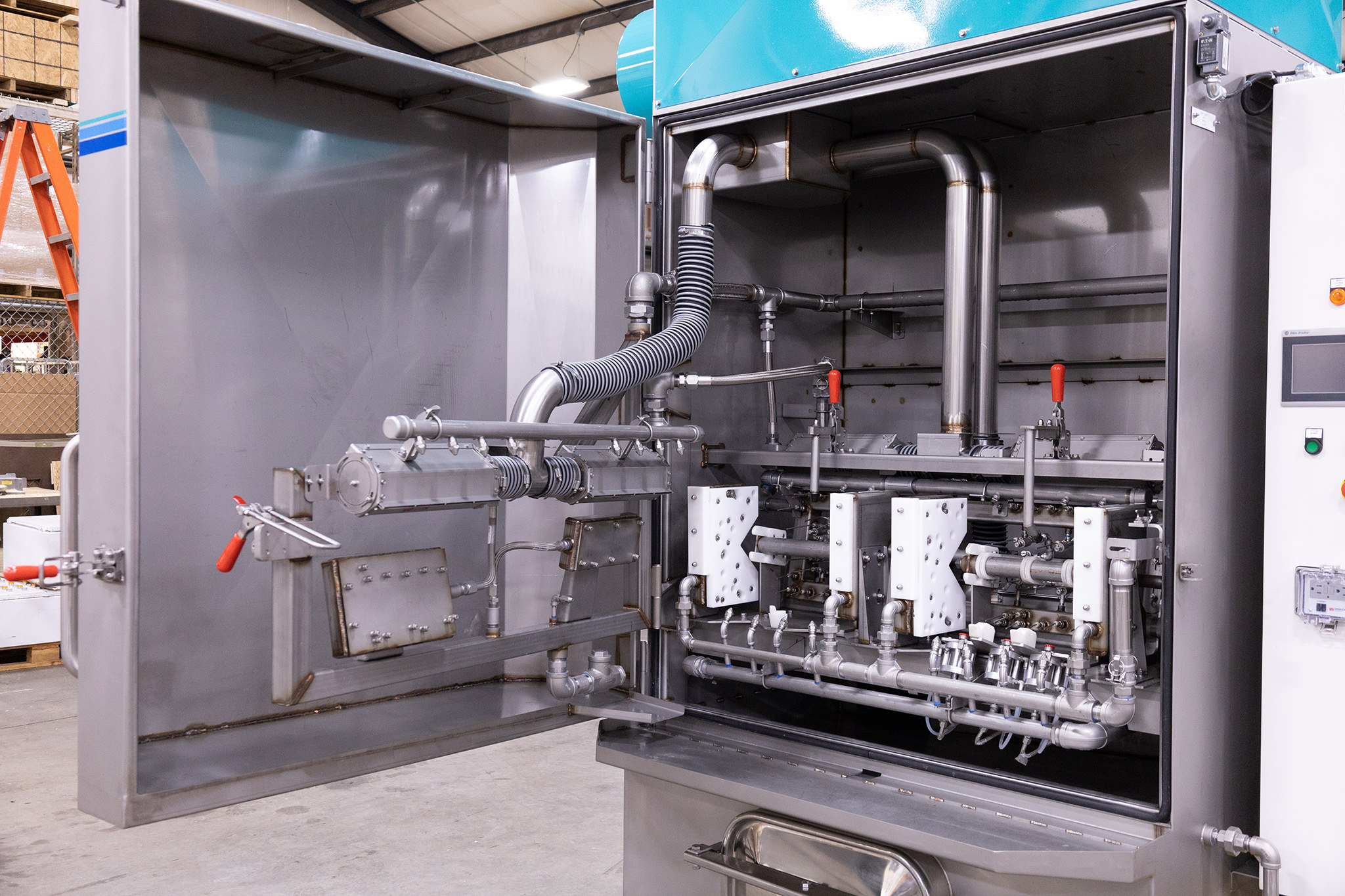
Solution
Alliance provided a stationary fixture machine for cleaning crankcases with heated wash and regenerative blowoff cycles. In addition to the general blowoff, a compressed air blowoff cycle was added to target critical part areas. The solution temperature will assist in further drying. The machine was programmed so that the same nozzles would be used for spraying wash solution and then for the compressed air blowoff cycle. Notable features of this machine include chemical injection, a contamination sensor for fine filtration, and an oil skimmer.
