
Customer Background
The customer is a leading producer of medium-caliber ammunition cartridge cases for the US Department of Defense. They also produce metal parts for other ammunition products.
Challenge
The customer needed a cleaning system to clean lubricant, chips, and soils from 25mm and 30mm tapered steel ammunition shell casings for a military application. It needed to clean and dry 10,000 shells per an 8-hour day, with parts exiting visually clean and completely dry.

Solution
A dual-lane chain conveyor Aquamaster CC-2400E cleaning system was provided. This ammunition casings cleaning machine had multiple solution and blowoff zones. The custom part fixtures were designed to rotate the parts throughout the cleaning process, and the conveyors were pitched at an angle to allow for drainage from the interior of the shell casings. The wash and rinse systems are steam-heated. Included with the bullet casings cleaning machine was an exhaust fan system with variable speed drive, a 1″ belt oil skimmer, micro-filtration chamber with contamination sensor in the wash zone, a product shutdown sensor at the load end, and a condensate return pump system.
Cleaning Method
A flow-through aqueous cleaning system was required to meet the high production requirement and to interface with the customer’s material handling devices for efficiency and logistics.
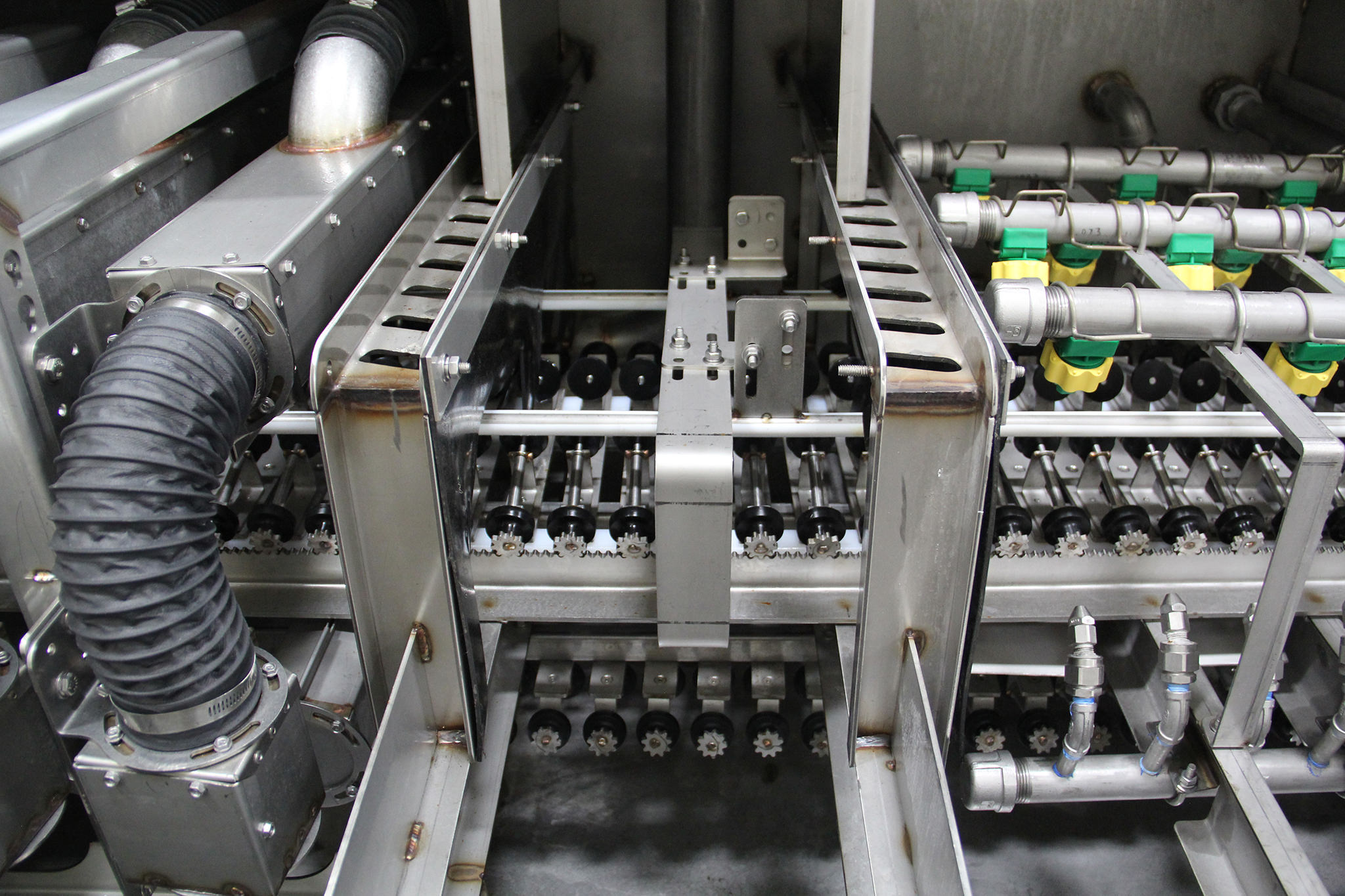