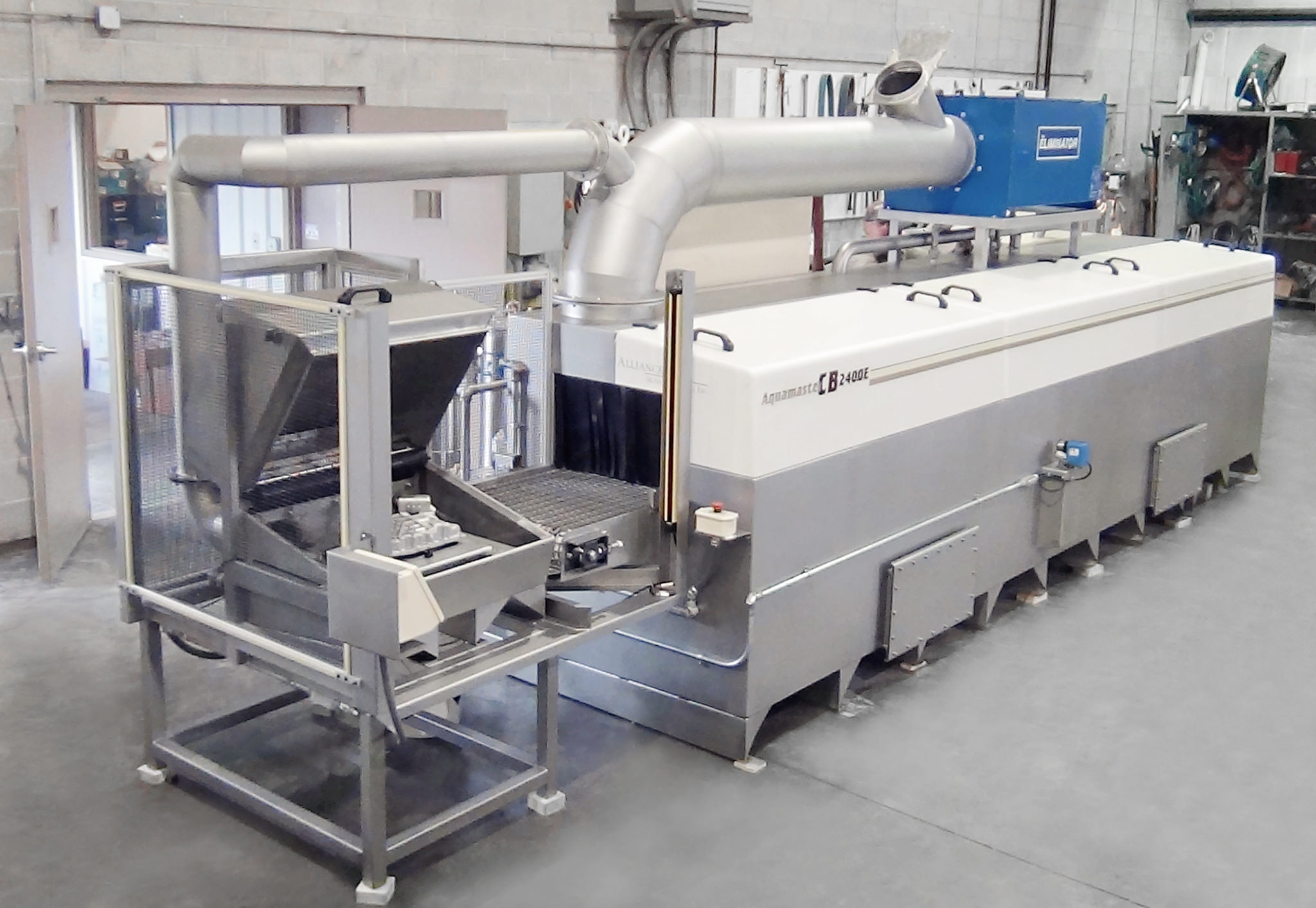
Customer Background
Customer is a manufacturer of die-cast aluminum and magnesium products for use in products in a variety of industries, including automobiles, trucks, power tools, electrical components, hydraulic pump bodies, cylinder liners, and transmission components. The company’s main goal is to produce products that are durable under heavy loads, leak-proof, and lightweight to increase fuel efficiency and allow tools to be lighter and easier for the user to operate. They specialize in utilizing magnesium as their lightest-weight metal in production. Operations are located in the United States and Asia.
Challenge
The customer was seeking an industrial transaxle rear cover washing system to remove coolant, burrs, and chips from the manufacturing process. Unlike other transaxle covers, this particular part had unique features such as cross-drilled channels that our customer was specifically concerned about. Loading and unloading would be performed robotically. The parts had to meet a stringent cleanliness standard including less than 2 mg of total mass. The transaxle rear cover is approximately 11” x 13”.
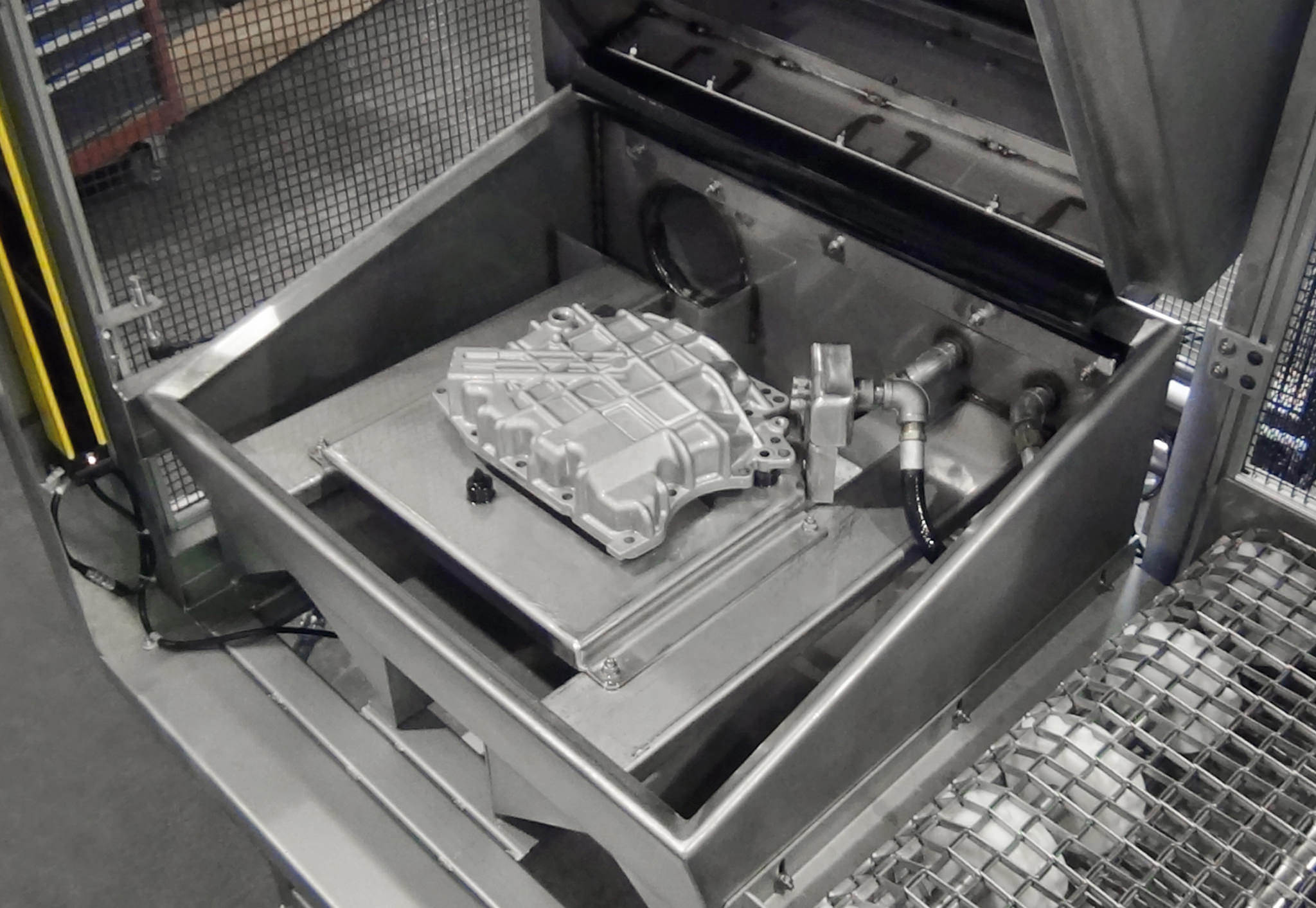
Solution
Alliance designed a conveyorized belt industrial parts washer to clean the transaxle rear cover, which included wash, intermediate blowoff, rinse, and blowoff modules. Strategically located spray nozzles ensure removal of hidden burrs and chips. The intermediate blowoff removes gross moisture prior to the rinse stage. Photo-eye product sensors located at the load end turn on the pumps and blowers in sequence. Conveyor speed can be adjusted by the user depending on production rates. A belt-type oil skimmer, mist collection system, and sound-dampening package were included options. Conveyor dimensional capacity is 24″ wide x 12″ high product opening.