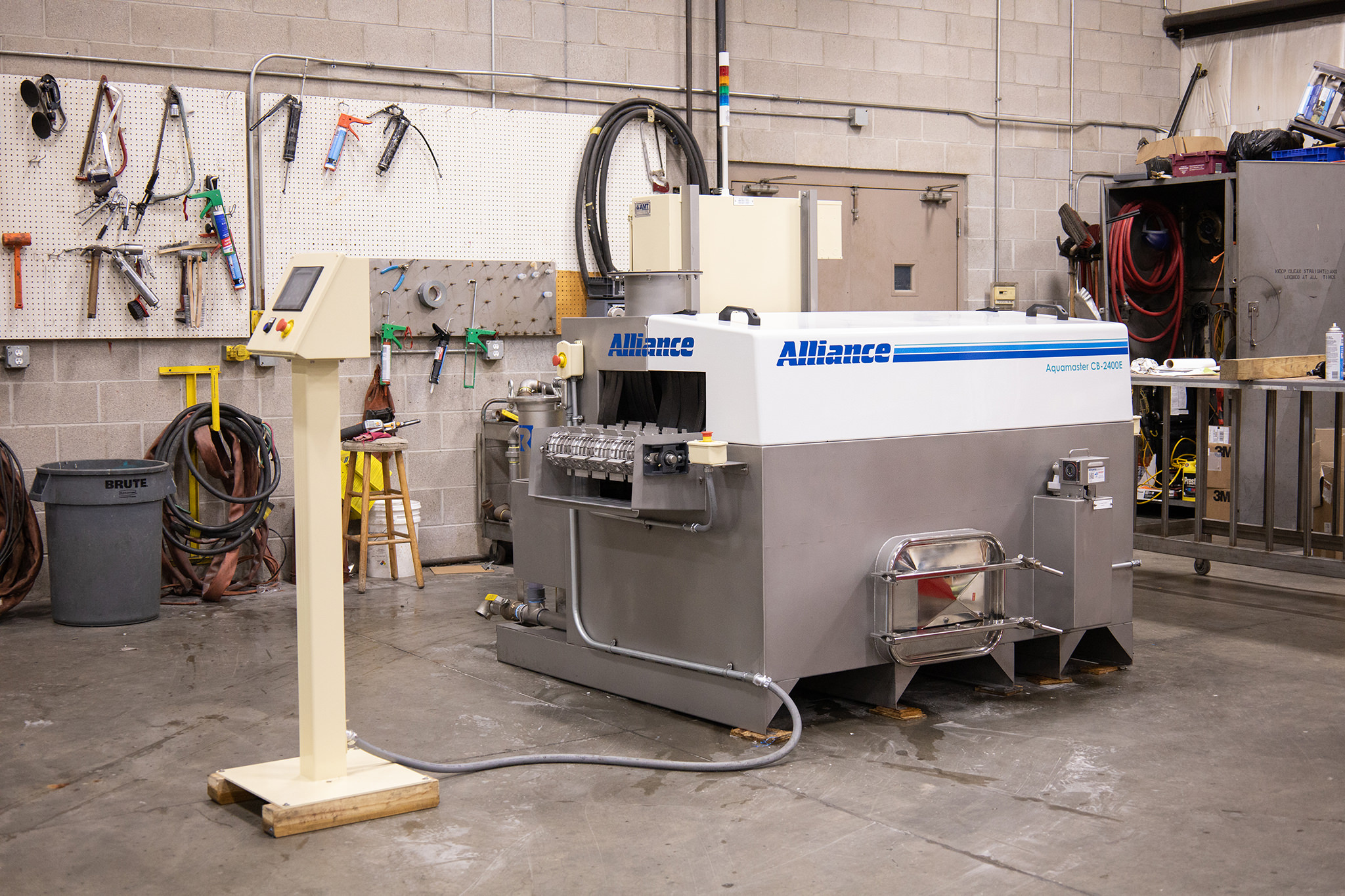
Customer Background
The customer is a producer of automotive shocks, struts, and related assemblies. They manufacturer of both OEM and aftermarket parts. The company’s US-based facilities primarily produce shocks and struts, while globally they also produce other automotive parts such as ride control, hydraulics, and electronics.
Challenge
The customer needed an inline washer to clean various sizes of shock tubes up to 18.9″ in length. The parts had a strict cleanliness specification and be visually free of oils, and needed to exit 100% dry or with residual moisture that would flash-dry quickly.
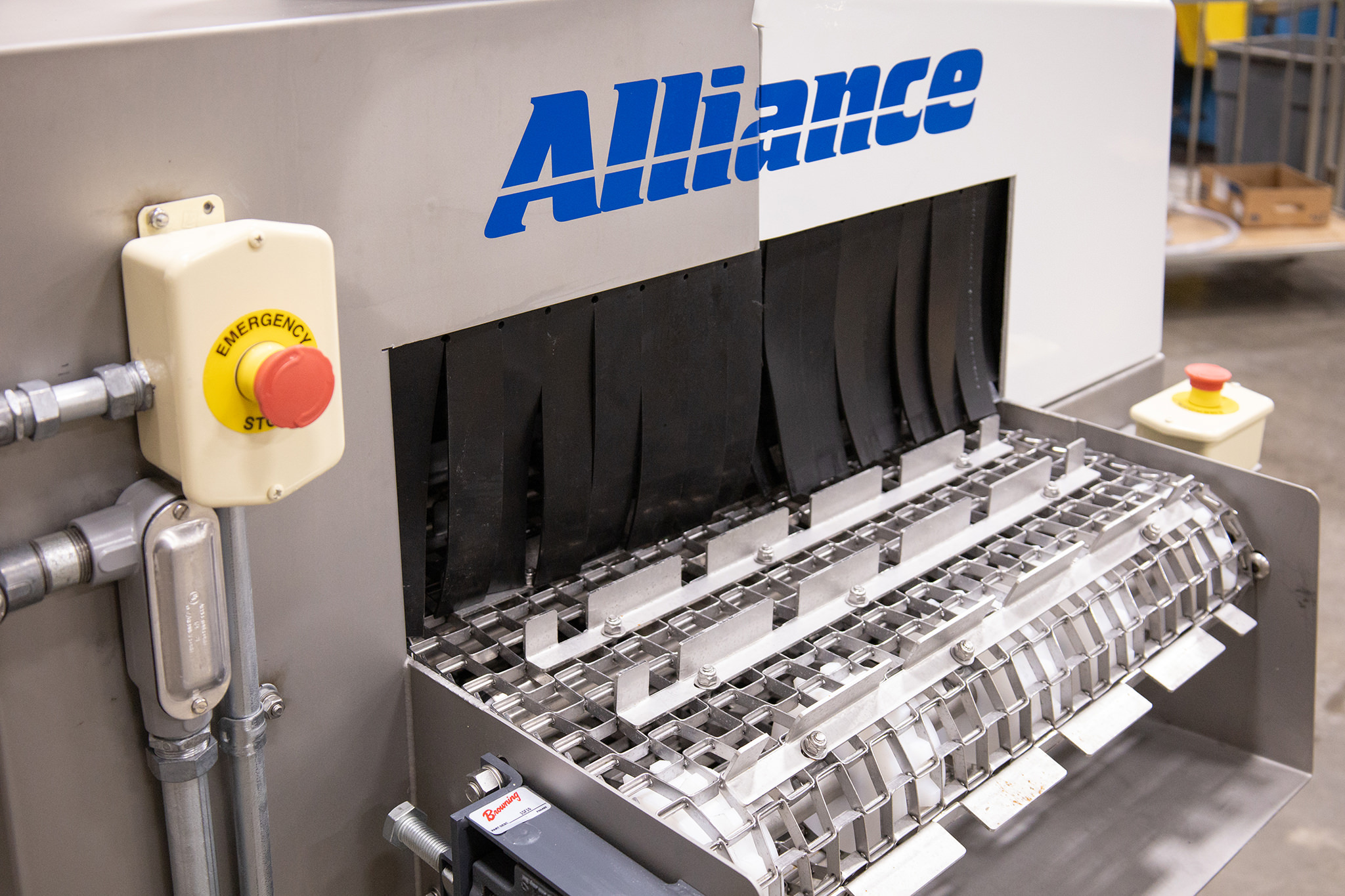
Solution
Alliance engineered a conveyorized belt inline cleaning system with wash and ambient blow-off zones. The conveyor belt is angled at 3° to aid in cleaning and drying, and a guide rail is installed on the low side to contain parts on the belt. The belt also has bolted flights to contain each part separately. Spray nozzles are located above, below, and to the sides of the conveyor. The air knives are also located above, below, and on one side. This inline cleaning machine’s components are made of stainless steel, and a micro-filtration chamber is included to remove fine contaminants. The HMI controls are remotely located on a sub-panel.
Cleaning Method
Inline aqueous cleaning machine system was chosen as the ideal method for this shock tube application due to the size and orientation of the parts.
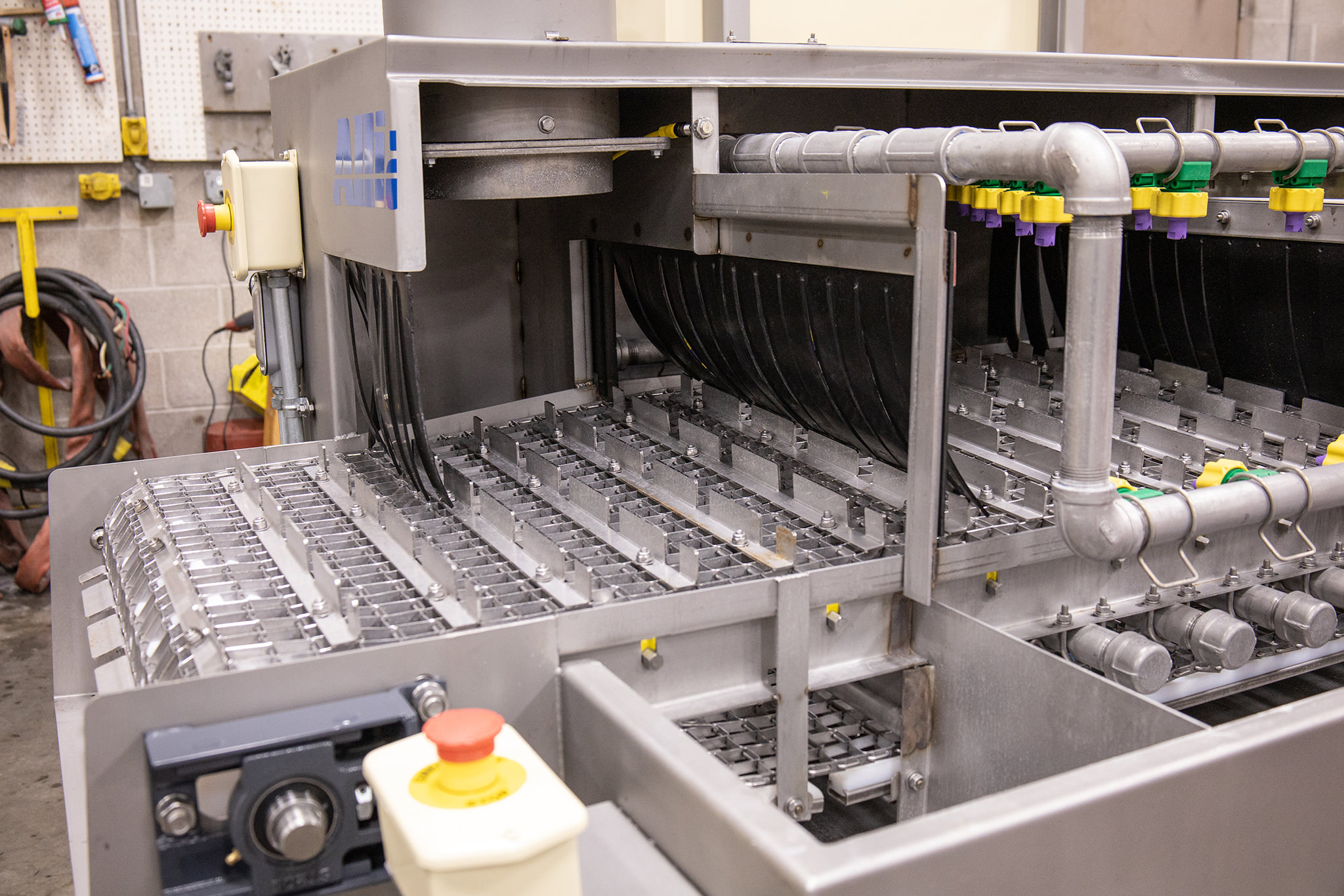