
Customer Background
The customer is a manufacturer of metal body parts, chassis parts, and plastic injection parts supplying automotive companies in the US and abroad. Their capabilities include metal stamping, welding assemblies, coating/painting, axle components, and plastic injection molding.
Challenge
The customer needed a washer to thoroughly remove soil, internal chips, and welding swag from multiple styles of tube assemblies which are part of an axle component. The interior of the tubes needed to be flushed, and there was a cleanliness specification of 10 mg maximum residual contaminant per component. Parts needed to exit the machine as dry as possible. The required cycle time was one part every 60 seconds.
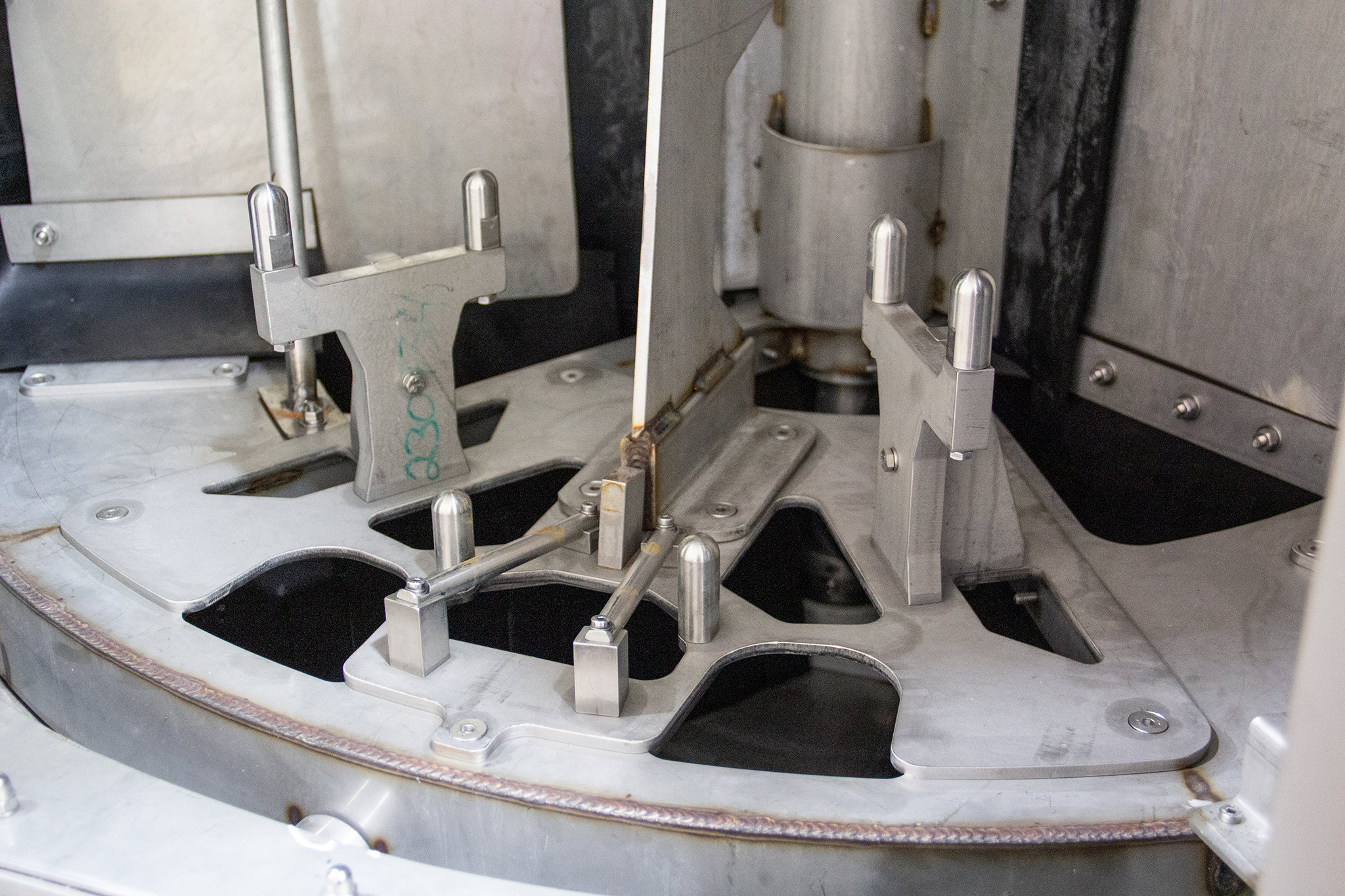
Solution
Alliance Manufacturing engineered a rotary indexing washer to clean the parts in cycles. Soiled parts are loaded and unloaded from a single location using a robotic automation and sensors to indicate load/unload. Strategically positioned spray nozzles thoroughly clean the interior and exterior of the tubes and then blow off residual moisture. Three specially designed part holders keep the various styles of tubes held in place for optimum cleaning in each index position. Cycle time is programmable via the HMI, depending on desired production rate and soil level.
Cleaning Method
Aqueous cleaning is the preferred method for this project. Robotic load/unload requires the parts to be placed onto a fixture in the same position each time. This style of machine also allows for cleaning and drying of multiple parts at a time. The large-sized parts are also better accommodated in an aqueous cabinet washer.
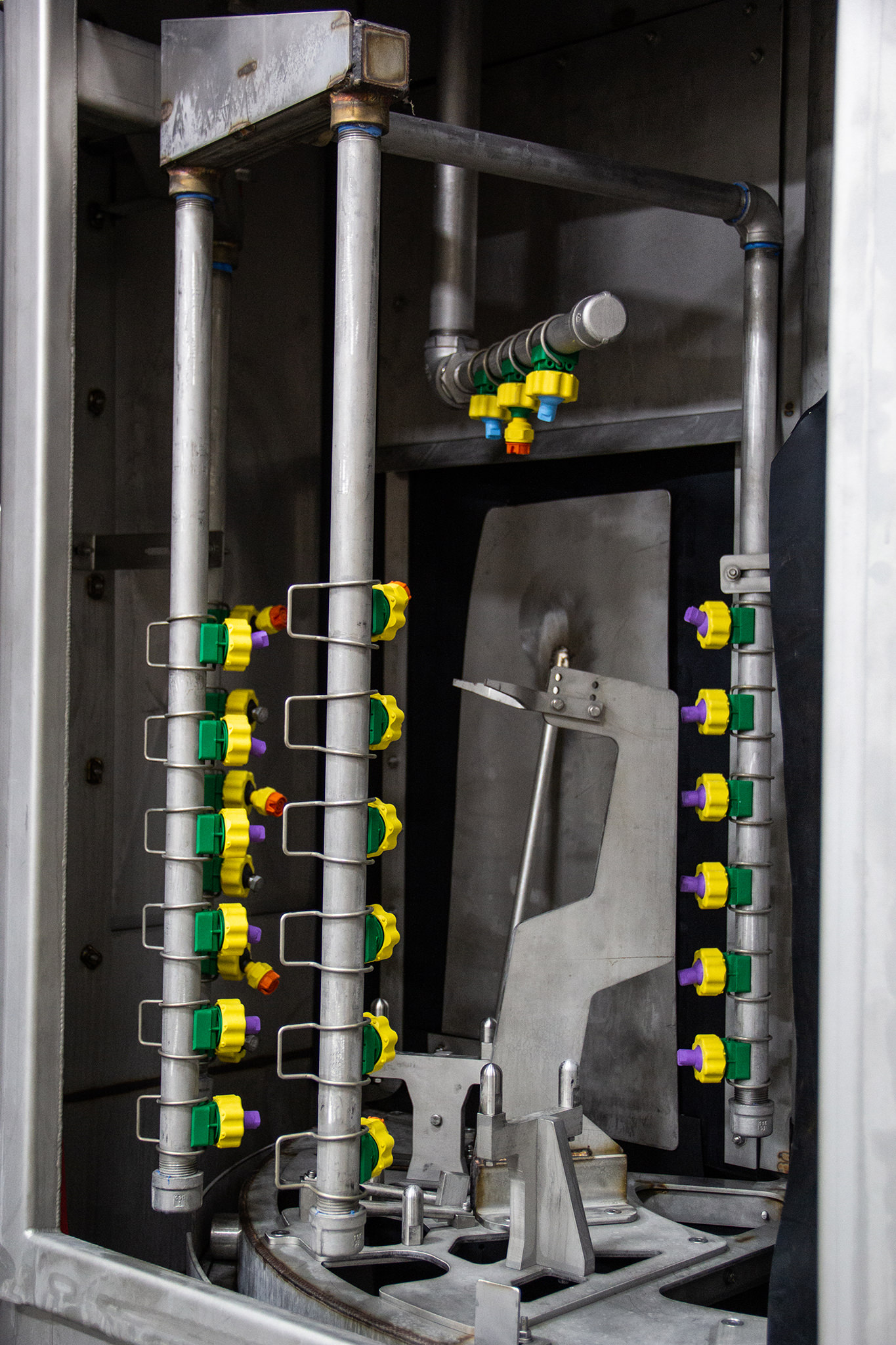