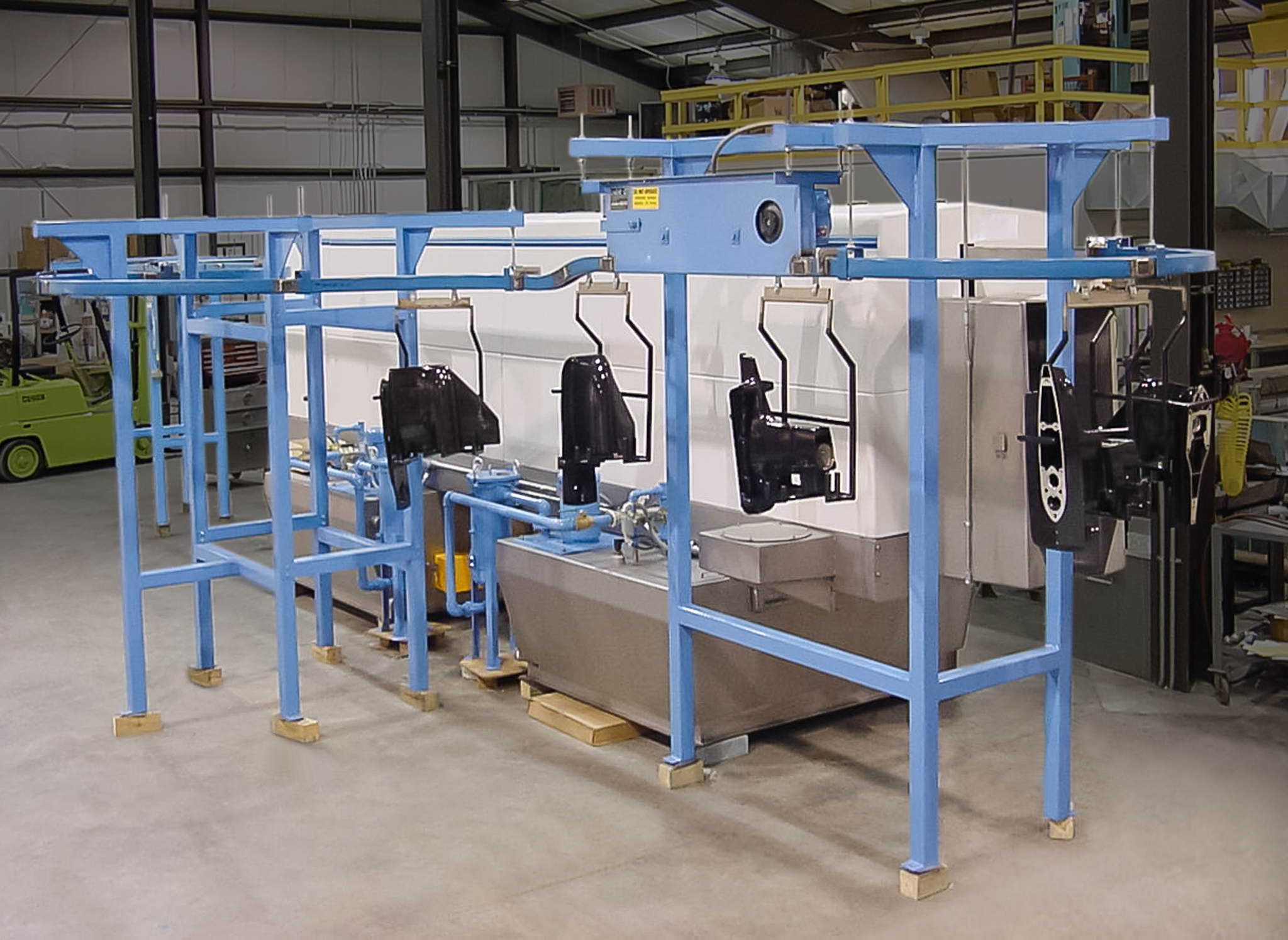
Customer Background
Founded in 1939, our customer is the largest U.S. based builder of marine propulsion systems.
Challenge
We were contacted by a team of engineers who were selected to purchase, install and fine-tune a new parts washing system. They required a cleaning system for seven different outboard gear case and drive shaft housings. The marine castings are made of stainless steel with an average weight of 30 lbs. The parts were coming directly from machining operations and contained significant amounts of particulates.
The current cleaning process utilized a dip tank with an agitation table for cleaning components prior to assembly. This process was very inefficient and required excessive material handling. The dip system did not remove the chips and floating contaminants were deposited onto the parts. After extensive research and testing, it was decided that they would move from the existing finishing method to a completely new process. Part of this new process was an improved automated cleaning system to remove the particulates, oils, and coolants before the chromate stage of production.
Solution
Several cleaning type systems were explored for this application. This customer was concerned about parts touching a conveyor belt in case of scratching so the decision was made to go with a conveyorized monorail system with custom designed part hangars. An Aquamaster CM-1800 was designed to clean the marine parts at a rate of 30 parts per hour.
This application required a heated wash, heated rinse, and ambient blowoff process zones. Both wash and rinse tanks have a 300-gallon capacity and are constructed of 10 gauge, type 304 stainless steel. Spray zones are 4′ 0″ long with multiple spray nozzles located on both sides of the conveyor tunnel. The electrically heated wash and rinse solution are recirculated for part cleaning. Externally mounted filter chambers hold a removable bag, which can filter particulate to a specific micron size.
The blowoff area is three feet long with a 15 HP pressure blower producing 1,400 CFM @ 19” of static pressure. A 360° monorail conveyor, supplied with the parts cleaning system, travels through the wash tunnel and loops around the exterior of the machine. The added conveyor on the exterior of the machine offers sufficient area for loading and unloading of the outboard gear case and drive shaft housings. The conveyor is adjustable from one to 40 feet per minute. Product sensors located at the unload end senses if a part remains in front of the eye longer than a designated length of time. If this situation occurs, the washer conveyor shuts off and will automatically restart when the photo-eye is cleared. A timer is located inside the control cabinet and easily adjusted for desired time duration. Machine functions are controlled by an Allen-Bradley SLC-500 programmable logic controller. Overall dimensions for this design are 22′ 0″ long x 6′ 6″ wide x 5′ 10″ high.