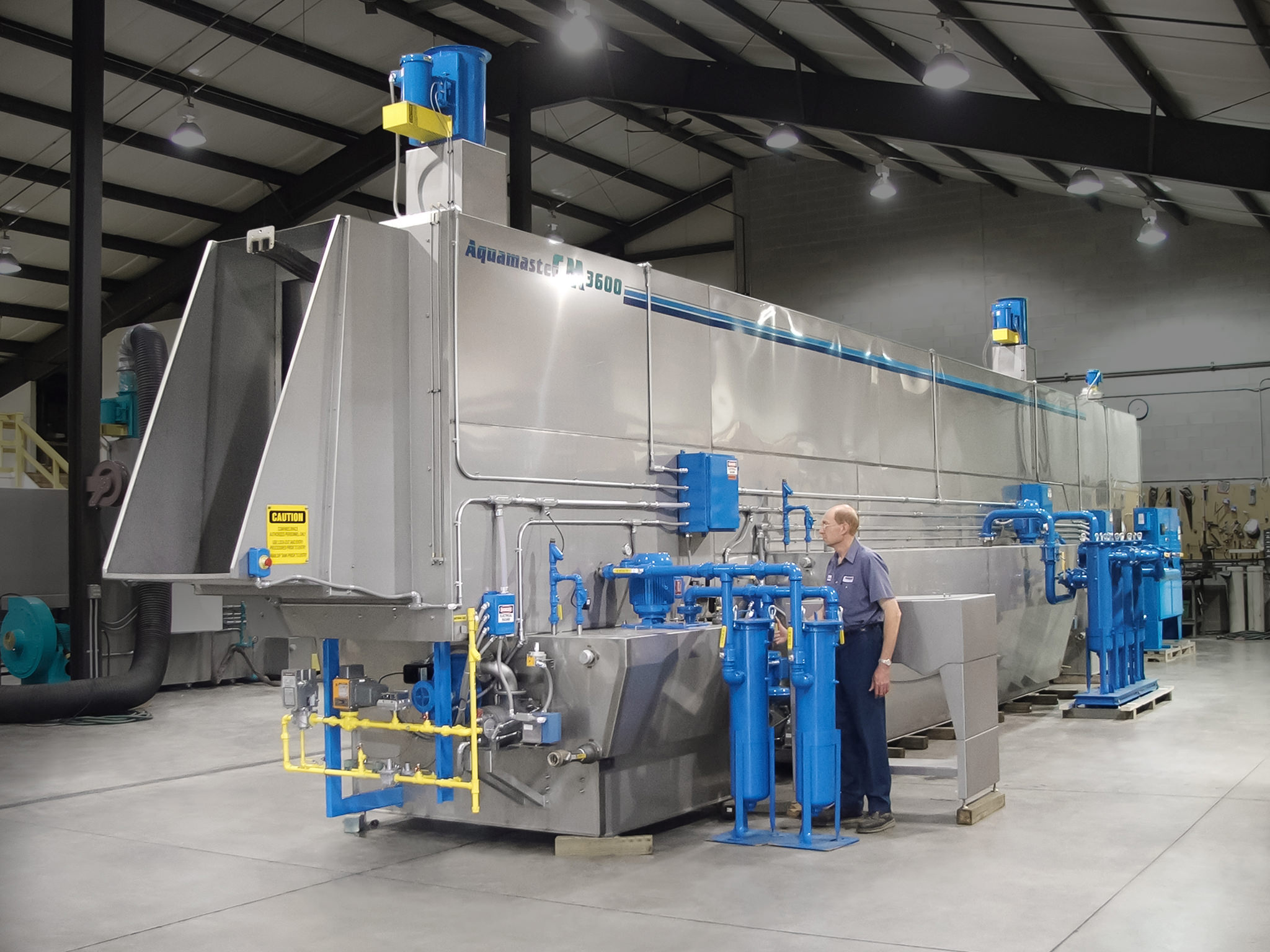
Customer Background
A leading global supplier of high-performance and severe-duty brake, clutch, transmission components, construction materials, commercial roofing, tire and wheel, heavy-haul truck trailer, food service, and data transmission industries. The company has manufacturing facilities in North America, Europe and Asia, and serves OEM and aftermarket customers in markets including mining, construction, military, agriculture, motorsports and aerospace.
Challenge
Customer required a cleaning system to be integrated into their monorail conveyor system for cleaning brake calipers and related components. Some components were to be transported through the process directly on hangers at a rate of 40 per hour; others, contained in baskets, at a rate of 20 per hour. Due to the configuration of the components, a submerged wash was required to insure cleaning of internal pockets, cavities, etc. Additionally, parts needed to exit the machine 100% dry, or as close as possible.
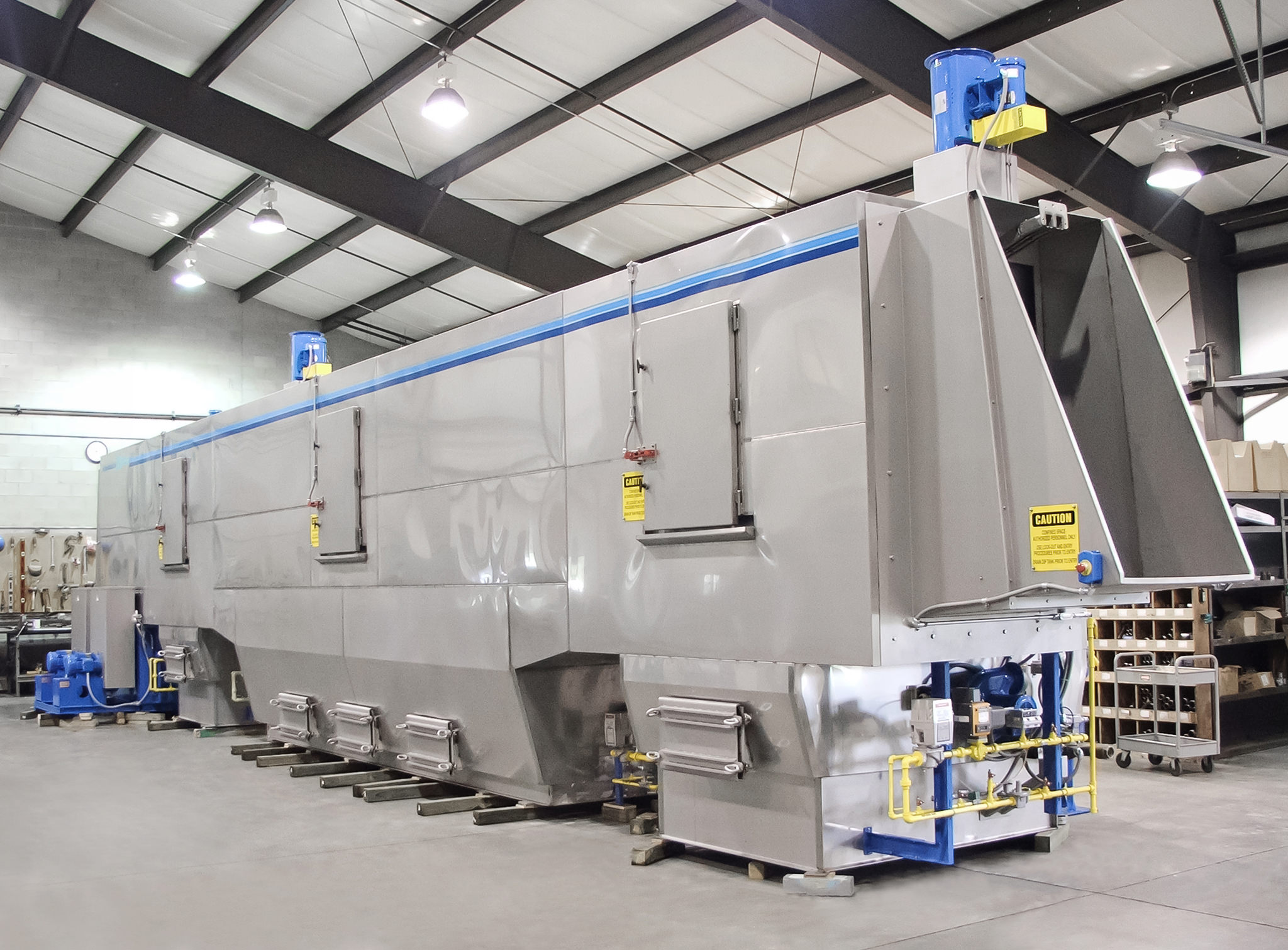
Solution
Alliance provided an Aquamaster CM-3600 monorail conveyorized parts cleaning system with pre-wash spray, submerged agitated wash, spray rinse and heated blowoff modules. The system utilized natural gas-fired burners for heating the pre-wash, wash, and rinse tanks and the heated blowoff air. The monorail system track within the machine transitioned in elevation to optimize the submersion depth and draining of product within the wash module. A stainless steel oil coalescing system was employed for the efficient separation of oils from the pre-wash solution.