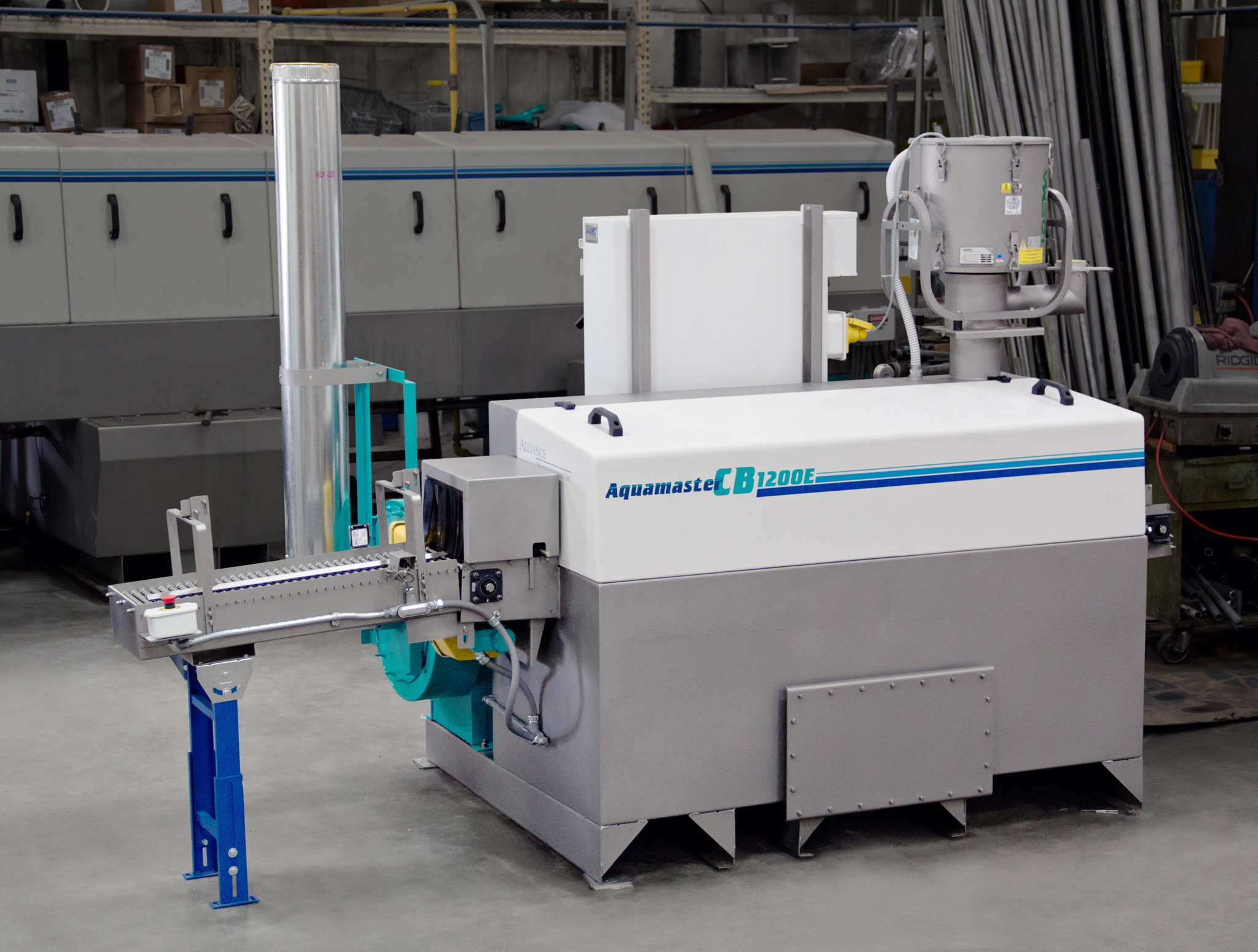
Customer Background
Customer is a leading manufacturer of oil pumps, fuel pumps, water pumps, and hydraulic systems. The product range includes lubrication, cooling, and fuel transfer pumps for industrial, and on- and off-highway diesel engines ranging from 1.5 to 30 liters. The company also provides engine front cover assemblies for agricultural and truck applications, and lubrication charge pumps for compressor and transmission applications. It serves the US and also other countries. The company maintains state-of-the-art facilities and processes based on lean manufacturing principles.
Challenge
The customer requested a machine to clean cast iron fuel pump housings and covers of varying sizes at a rate of 10 per hour. Parts were contaminated with soluble coolant, chips, dirt/dust/sand, and vibratory residue. Parts needed to be visually clean and rust-inhibited within one stage. Residual moisture was acceptable if parts would be dry within one minute after exiting machine.

Solution
Alliance provided an Aquamaster CB-1200E conveyorized belt parts cleaning system with heated wash and ambient blowoff modules. The conveyor was designed to have two product lanes, separated by an adjustable guide. Differing product types can be loaded onto either conveyor lane and remain separated throughout the wash process. A gravity conveyor was provided at the discharge end of the machine for part accumulation. A finger-style product transfer was included for smooth transition of parts from the wash conveyor to gravity conveyor. A photo-eye sensor at the top of the gravity roller conveyor senses when the accumulation is full and stops the conveyor to prevent overloading. Adjustable nozzles are positioned above, below, and to the sides of the conveyor in the wash zone. Multiple adjustable high-velocity air knives are located in the ambient blowoff zone. Some of the optional accessories included a mist collection system, micro-filtration, and photo-eye product sensors. Machine was modeled after another Alliance parts washer previously purchased by the company.
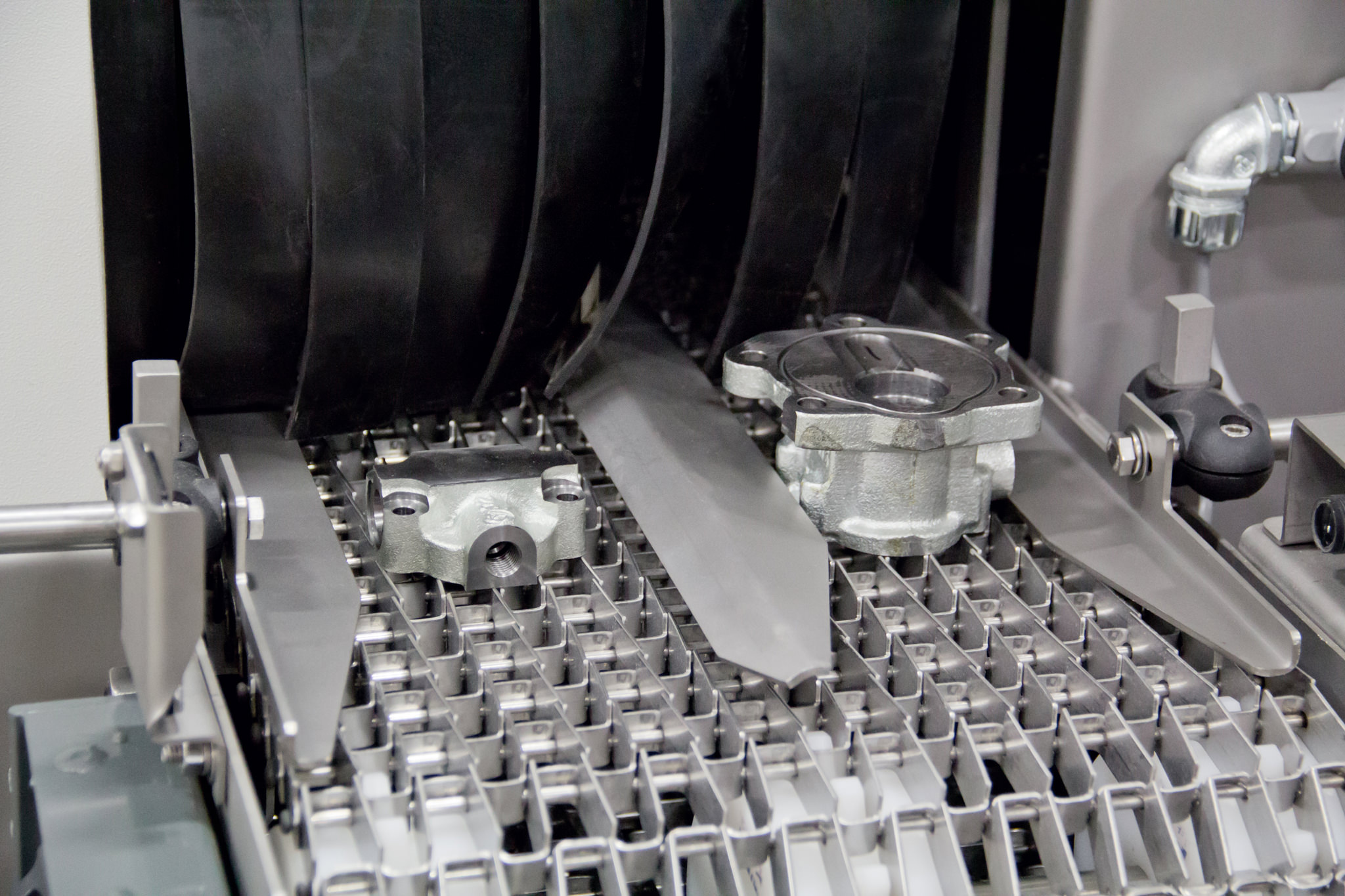