
Customer Background
Manufacturer of fine blanked, deep-drawn, and progressive stamped metal parts made from aluminum, steel (stainless, cold-rolled, galvannealed, nickel-plated), brass, and copper. Items are manufactured for a variety of industries, primarily in the automotive and industrial markets.
Challenge
The customer was seeking a washer to remove stamping lubricants and other light manufacturing soils from a variety of fine blanked parts, at a rate of 124,000 in2/day single layer in parts baskets. A strict cleanliness standard of 10mg/1,000 cm with no particles larger than 400µ was required. The customer wanted the ability to load both rotational and non-rotational baskets and have the parts washing baskets returned to the loading area of the machine.
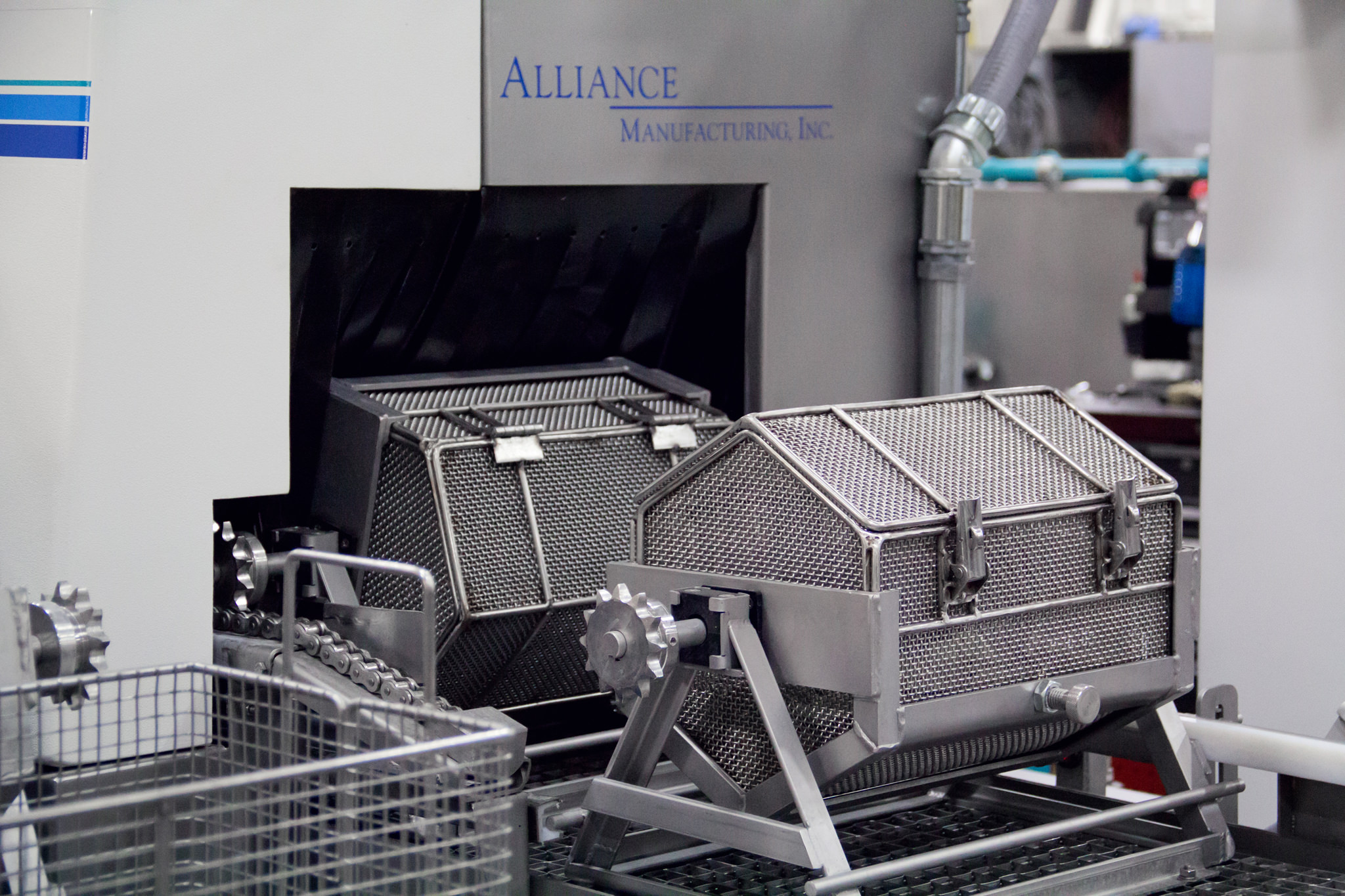
Solution
Alliance provided an Aquamaster CB-1800E indexing conveyorized washing system with a specialized rotating parts washing basket conveyor system. The machine included wash, rinse, rust inhibit, and heated blowoff modules. Parts are placed into either rotational or stationary (non-rotational) baskets. The rotating parts washing baskets are hexagonal in shape and are constructed of stainless steel. Rotational baskets were designed with two perforation sizes to accommodate varying parts sizes to be cleaned. Rotational baskets are placed by the operator into a carrier frame with gears to guide rotation via stationary chains on either side of the conveyor belt. Parts that do not need to be tumbled can be placed in standard baskets directly on the conveyor belt. A 180° return pop-up transfer conveyor at the unload end of the machine raises baskets and transfers them onto a powered roller conveyor and then on to a gravity accumulation conveyor. The accumulation conveyor returns the washed parts in baskets back to the operator at the load end of the machine. This versatile machine gave the customer the ability to wash, rinse, rust inhibit and dry a wide variety of fine blanked parts either in rotational baskets or stationary baskets directly on the conveyor belt.
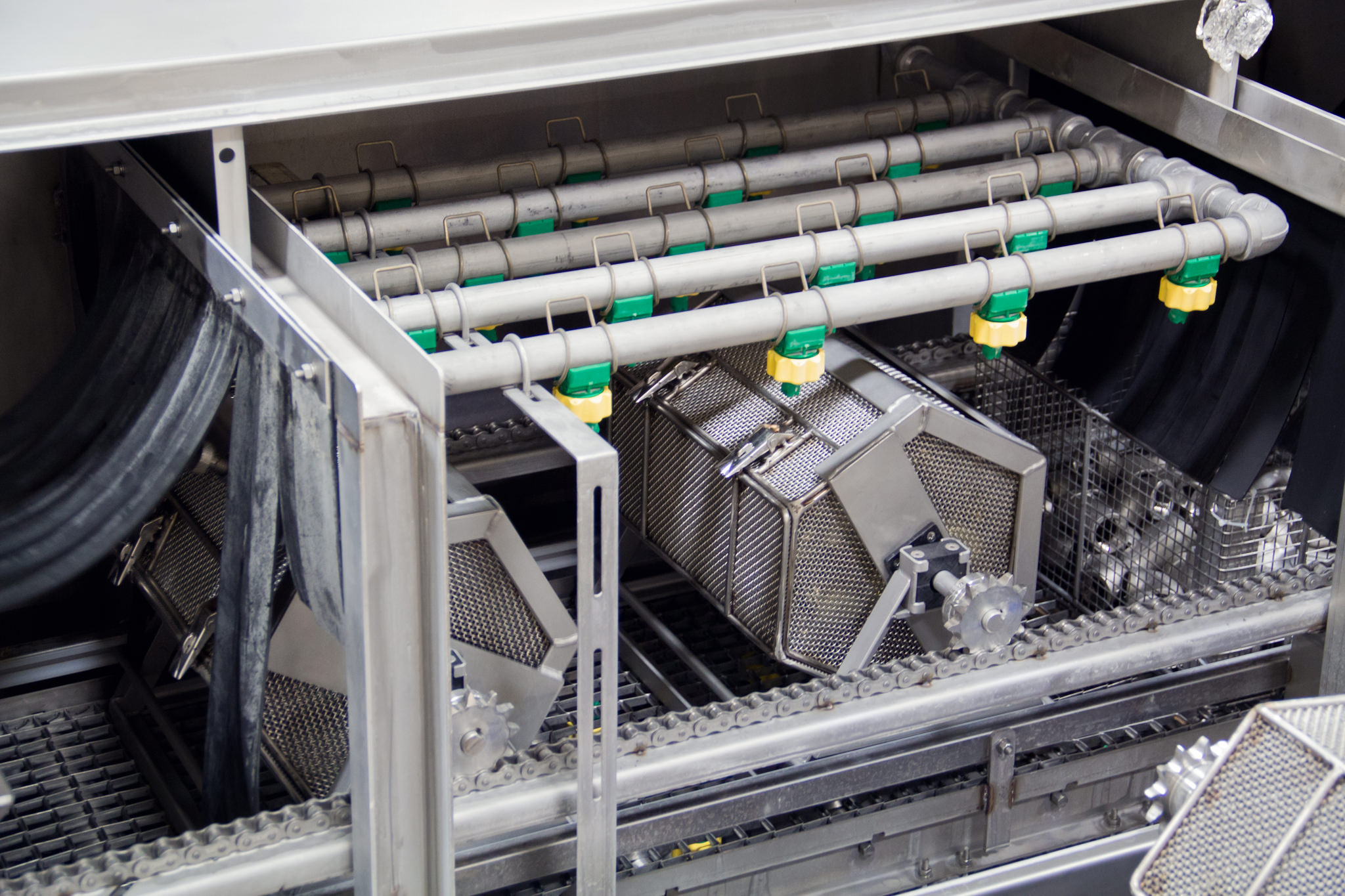