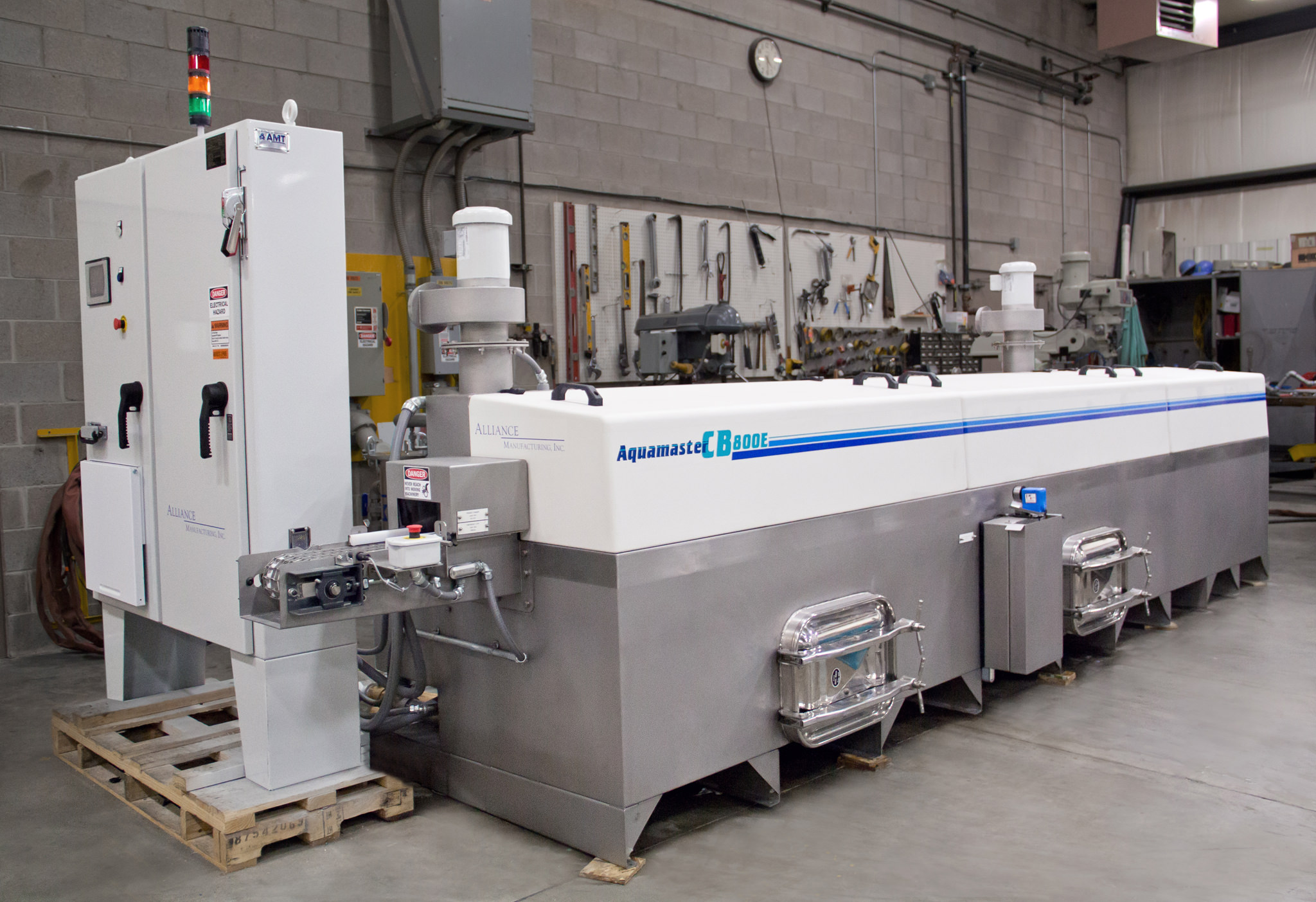
Customer Background
The customer is a producer of metal-formed components and assemblies for many automotive manufacturers, primarily OEM and Tier 1 companies. They have plants in 13 countries and are one of the largest suppliers in the industry. Their focus is on creating more efficient products while improving vehicle performance for the end user.
Challenge
The customer was seeking a solution for cleaning automotive connecting rod parts. The smallest rod is approximately 170mm long x 70mm wide and the largest rod is 215mm long x 85mm wide. The washer needed to be able to clean various sizes at the same time. The target production rate was approximately 3.7 million parts per year running 22.5 hours/day over 240 days/year. The final cleaning results had to adhere to a specification of 5mg total mass and 500 micron largest particle size or smaller, and were required to be 100% dry upon exiting the machine.
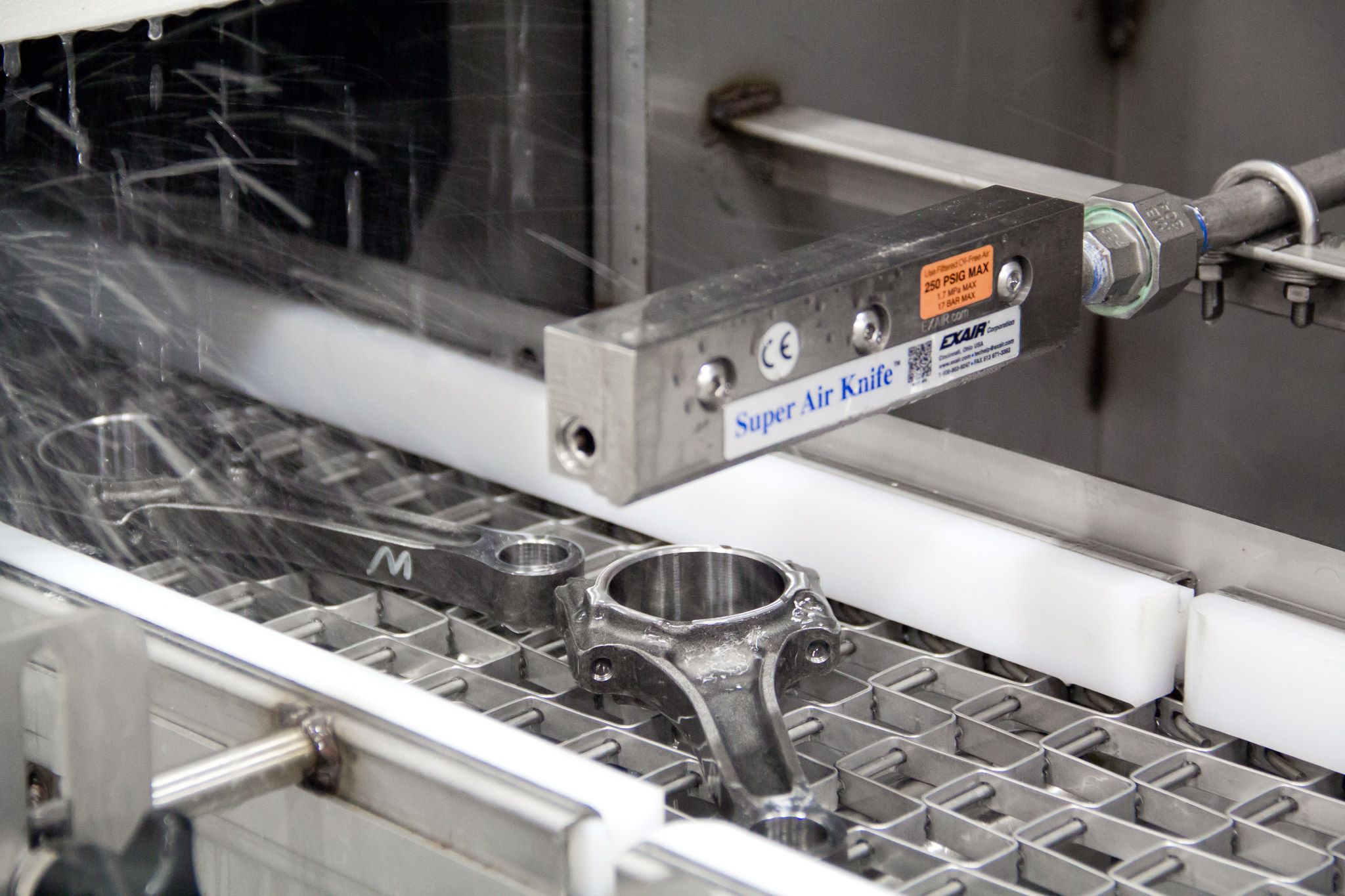
Solution
Alliance provided an Aquamaster CB-800E parts cleaning system with wash, intermediate blowoff, rinse, and ambient blowoff modules. The automotive connecting rod parts were transported on an 8” wide stainless steel conveyor belt with product guides running the length of the machine. The conveyor was set at a speed of approximately 7.6 ft./min., allowing for a production rate of 720 rods/hr. Conveyor speed is adjustable to accommodate varying production rates. High-velocity air knife systems, located above and below the conveyor, are used in both the intermediate and final blowoff stages. Couplings were added for possible future use of a compressed air blowoff. An exhaust fan with condensate return, dual mist collectors, a belt-type oil skimmer, and a photo-eye product sensor at the load end were selected options. A sump pump system was included for evacuating spent solution from the machine. Hinged cleanout doors were used in place of bolt-on doors to allow for better efficiency when performing routine maintenance tasks. Overall dimensions are 22’2” long x 4’6” wide (6’4” wide at blowoff blower sound enclosure) x 4’3” high (6’3” to top of control panel). A custom paint scheme was used to match customer operation colors.
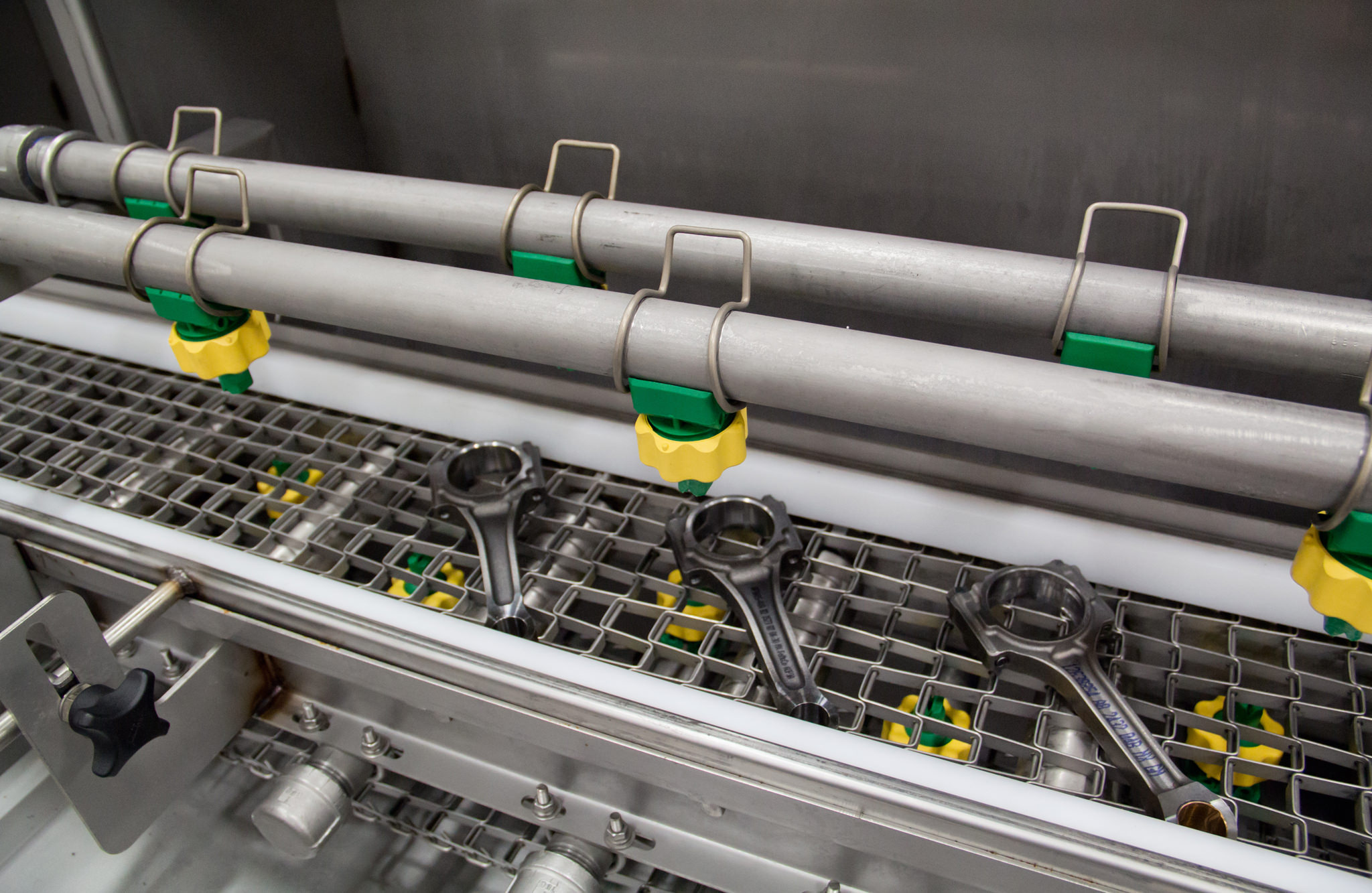