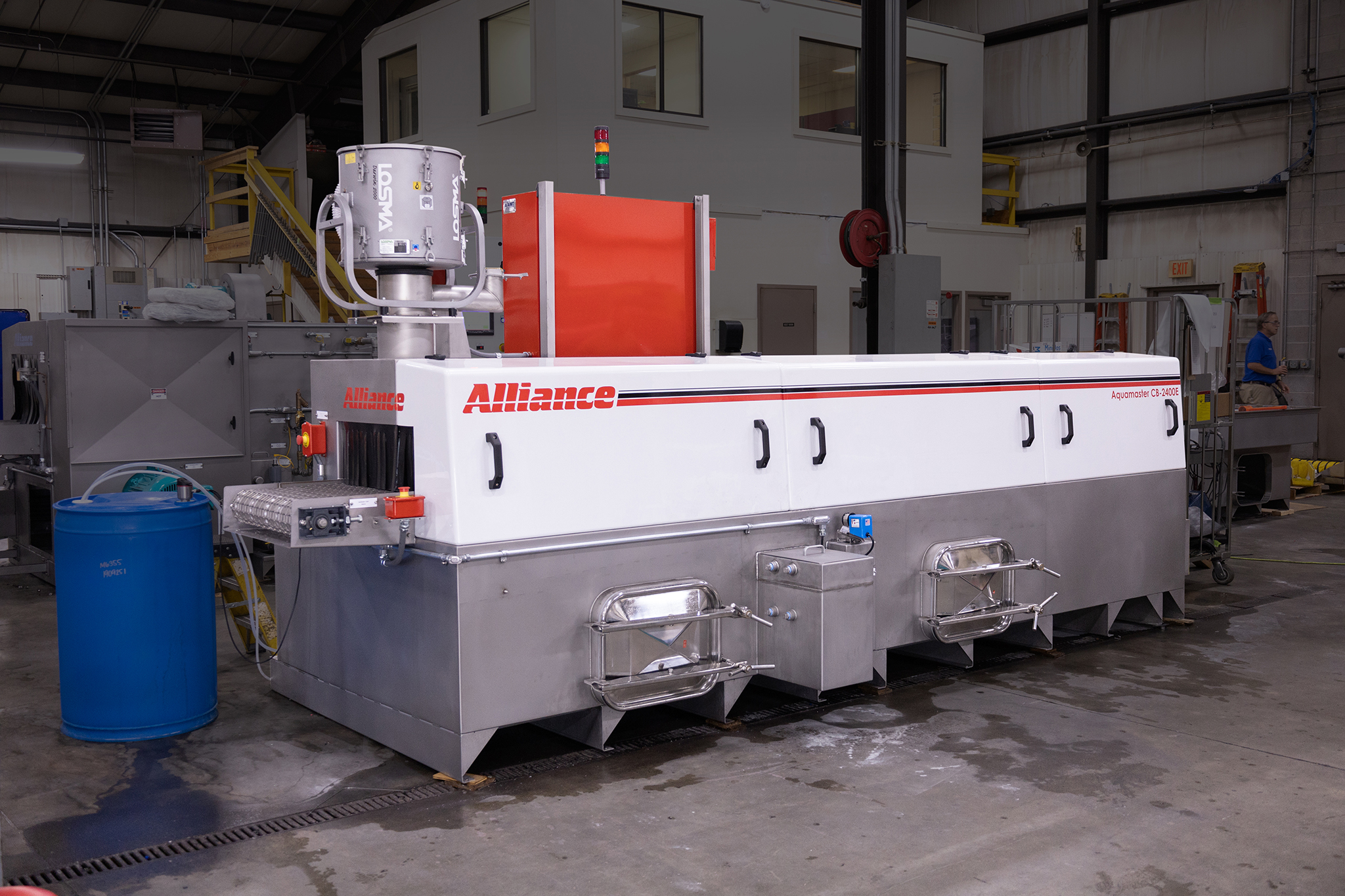
Customer Background
The customer is a provider of various tools and measuring devices for use in the building trades. It is a subsidiary of a larger, well-known tool company. The cleaning application was for rafter squares branded for both companies.
Challenge
The customer needed a cleaning system to remove soils from multiple sizes of aluminum rafter squares before the next manufacturing process. The rafter squares come anodized and with a clear coat already applied. During a cutting process which takes place prior to cleaning, they are held down firmly with clamps, which leave a black residue on top of the clear coat surface. Cutting oils are also present. As a result of the cutting process, some aluminum chips may be present near the raw cut aluminum edges. The most challenging part of the equation is that the clear coat is heat-sensitive.
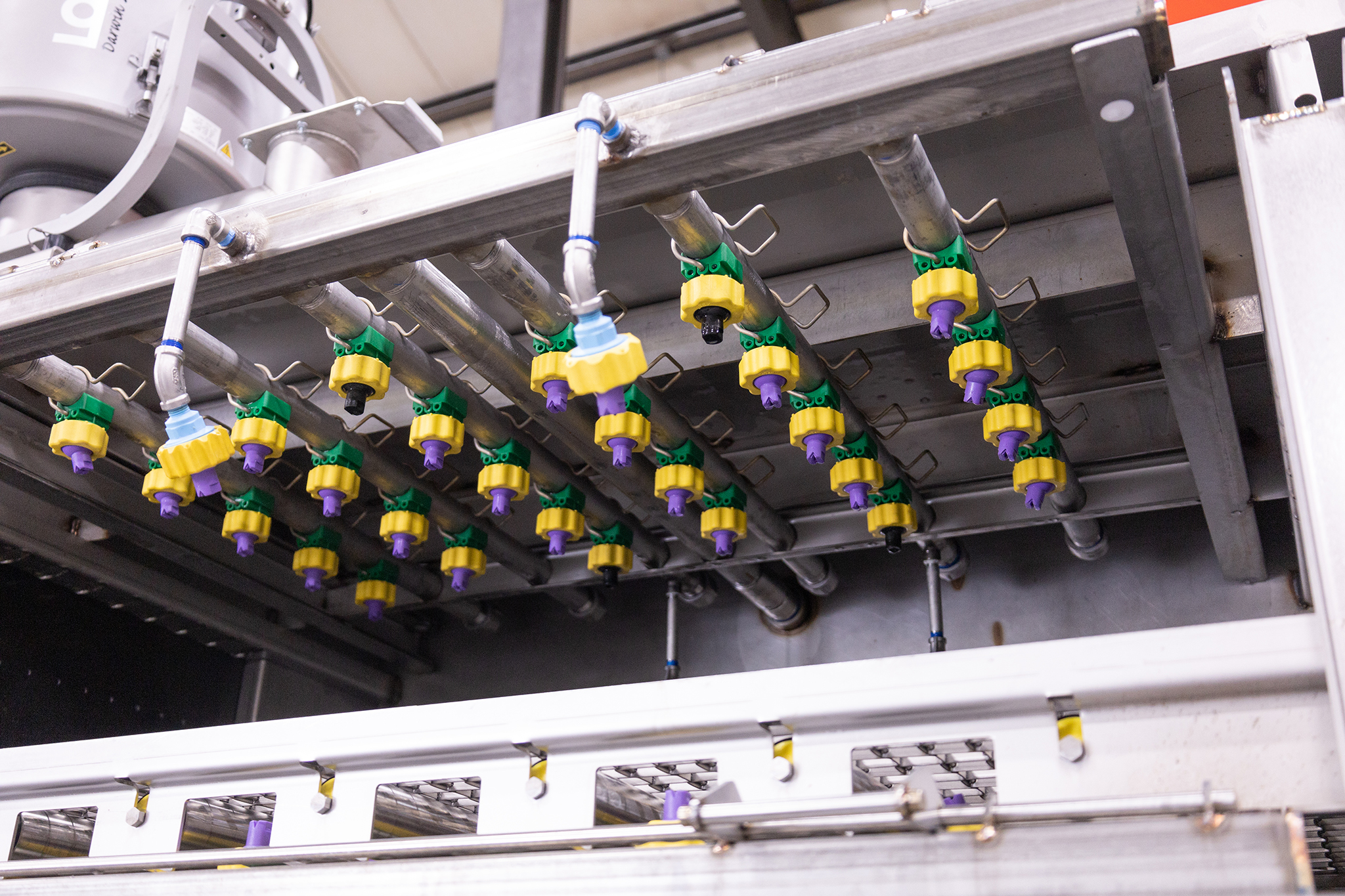
Solution
Alliance provided a conveyor belt cleaning system with wash, rinse, and heated blowoff zones. Due to the heat sensitivity of the clear coat, the wash, rinse, and blowoff heat was set to not exceed 120 degrees F. To keep the lightweight parts from moving out of position on the conveyor belt, spray pressure was set slightly higher on the upper sprays and low on the lower sprays.
Cleaning Method
Aqueous cleaning was selected as the best option due to the high volume requirement of the application, the need for a continuous inline process, and the low temperature requirement to prevent degradation of the clear coat.
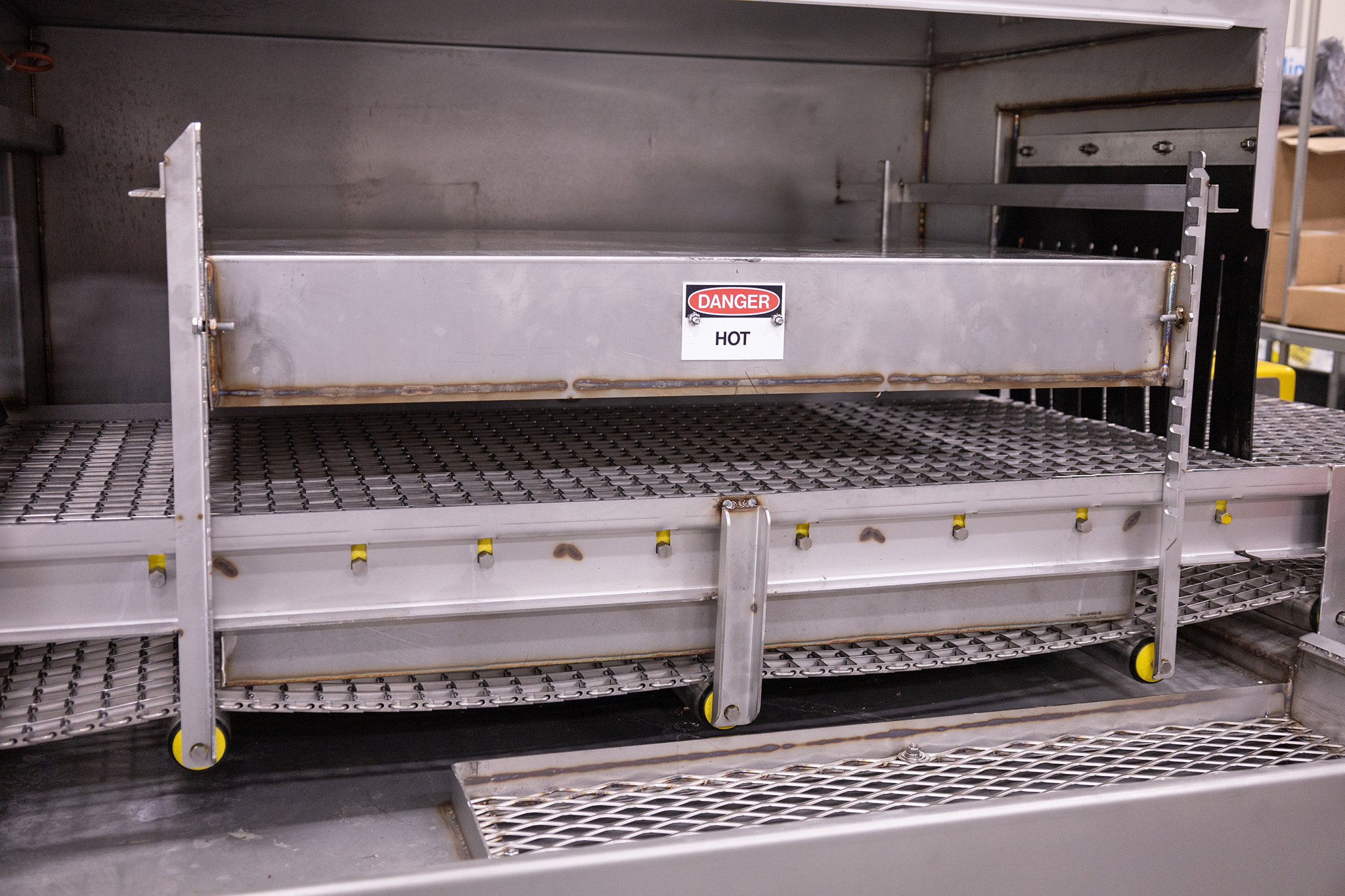