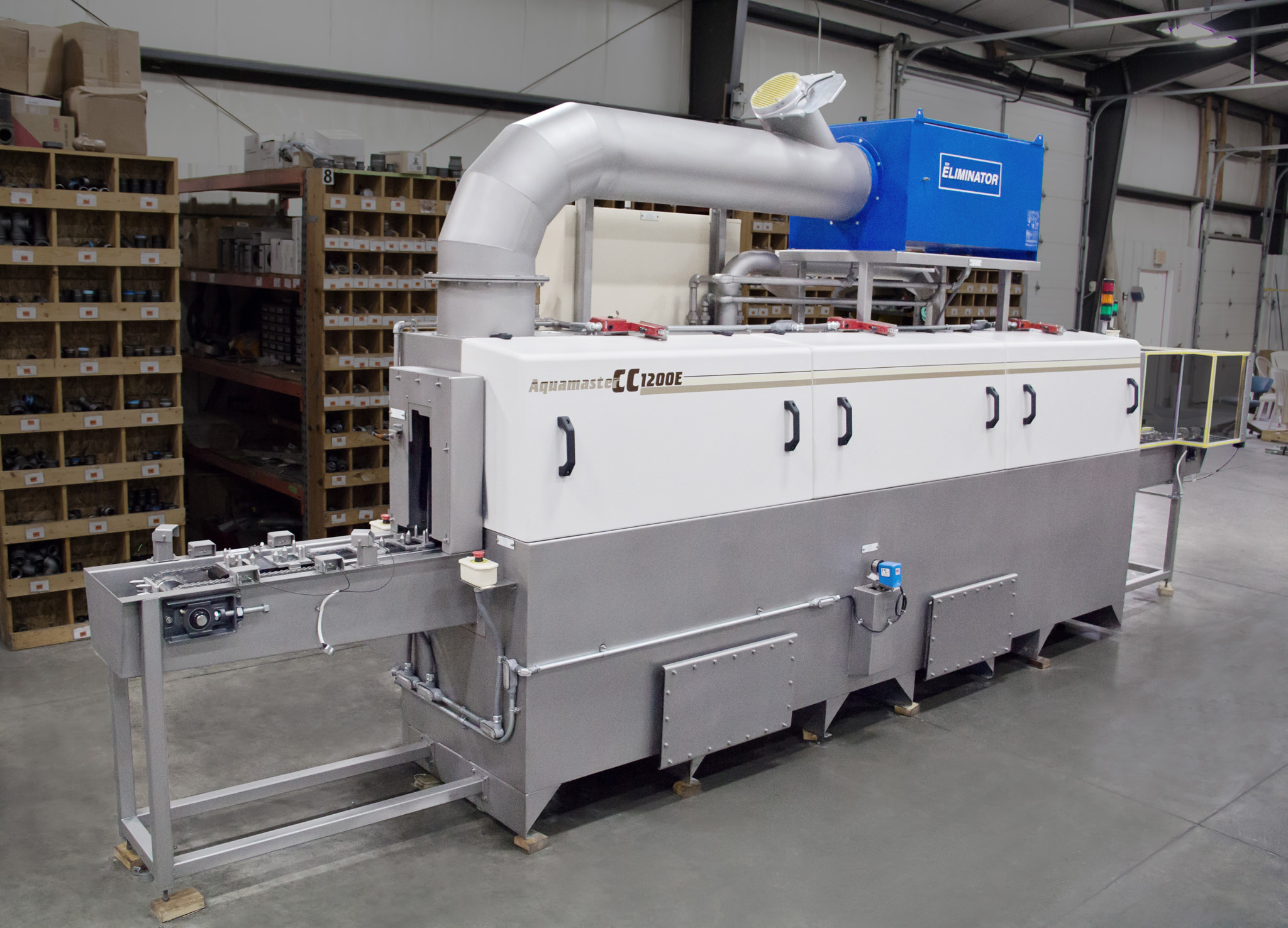
Customer Background
The customer is a manufacturer of die-cast metal products for use in a variety of industries. The company’s goal is to produce products that are durable under heavy loads, leak-proof, and lightweight, to reduce the overall weight of the application that uses their products. Their products are used to increase fuel efficiency and allow tools to be lighter and easier for the user to operate. They specialize in utilizing magnesium as their lightest-weight metal in production. Operations are based in the United States and Asia.
Challenge
The customer was in need of a parts washer to remove coolant and chips from their manufactured metal oil pan for a major automobile manufacturer. The aluminum automotive oil pan parts had to be 100% dry upon exiting the cleaning system, be below 110 degrees Fahrenheit, and meet a stringent cleanliness standard. Single part flow was required for automatic loading and manual unloading.
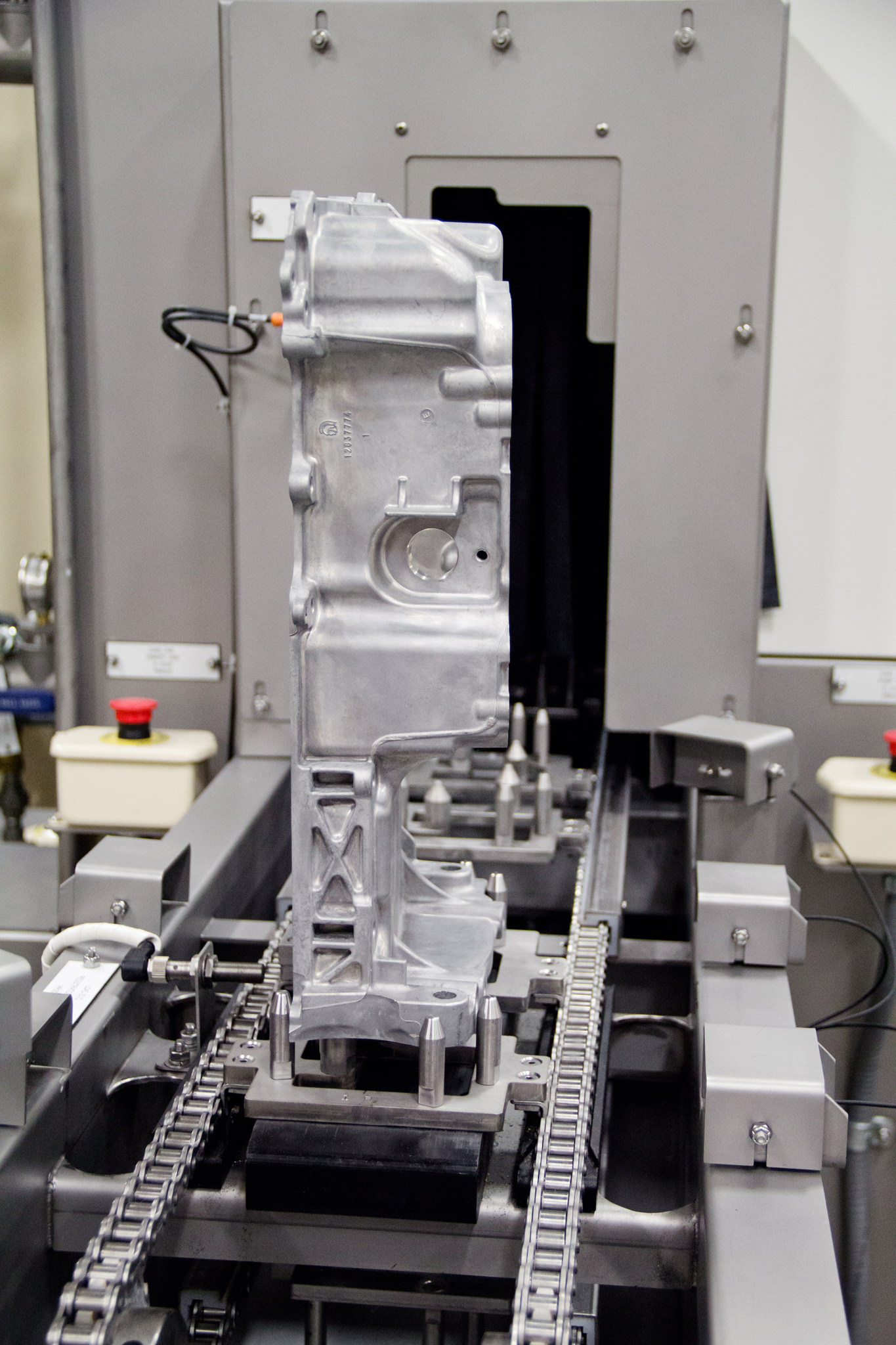
Solution
Alliance provided an Aquamaster CC-1200E conveyorized indexing parts cleaning system with wash, intermediate blowoff, rinse, and ambient blowoff modules. The conveyor is 12″ wide with an 18″ high product opening. The start/stop indexing conveyor system is ideal for cleaning and drying specific part features and blind holes. Index cycle time can be programmed based on production rate of parts. A part profile plate was incorporated at the load end of the machine to disable the conveyor in the event of a loading error. The oil pan cleaning system is set up for pick-and-place part loading and manual unloading. Mesh guarding and light curtains were recommended at the unload end for operator safety. Photo-eye sensors located at entrance and exit of the oil pan cleaner ensure accurate part positioning for part load/unload. A customer-specified mist collector was incorporated into the design. Alliance’s Full-Access fiberglass canopy segments were included for easy access to the interior for maintenance and process adjustment.
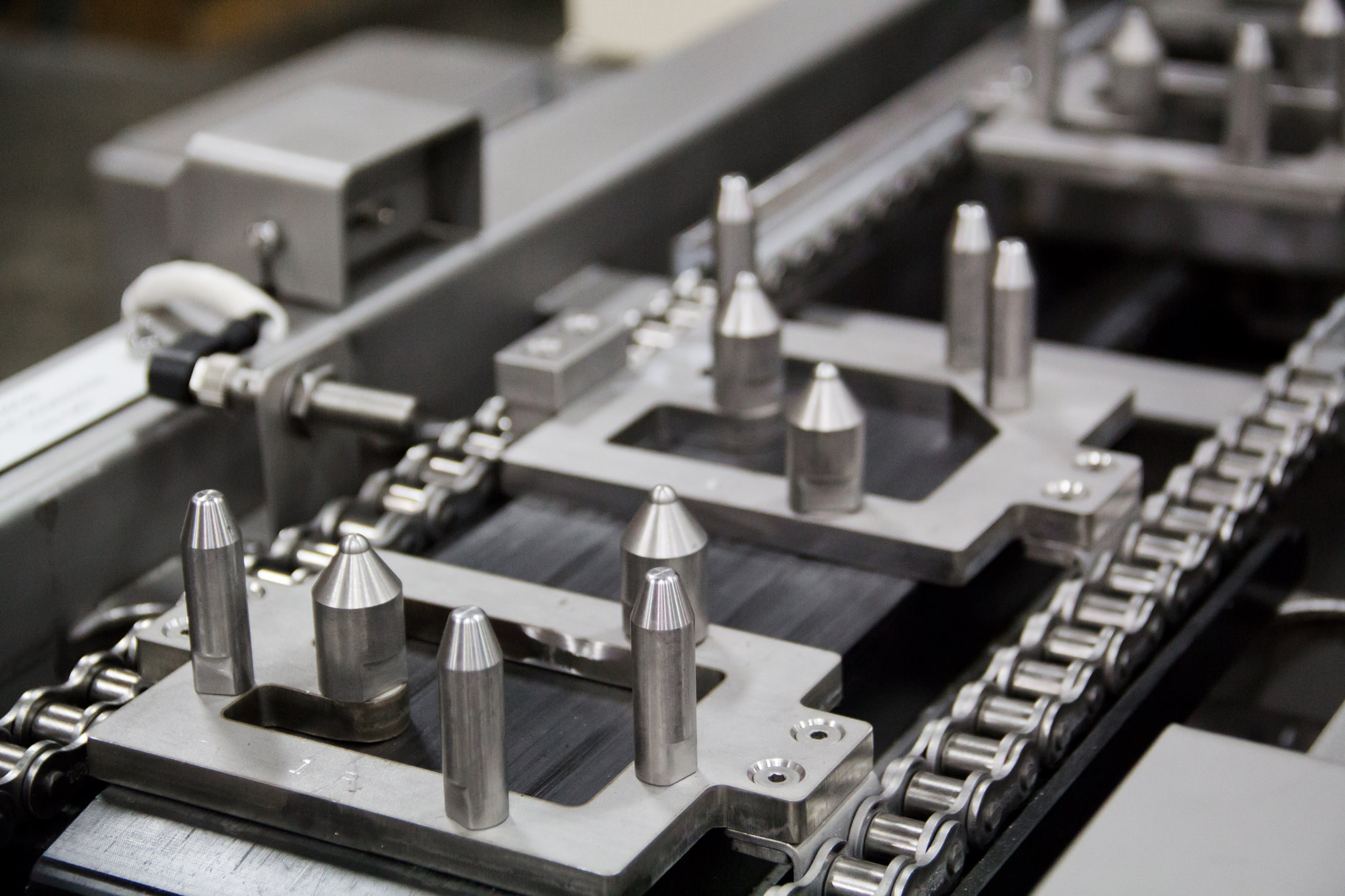