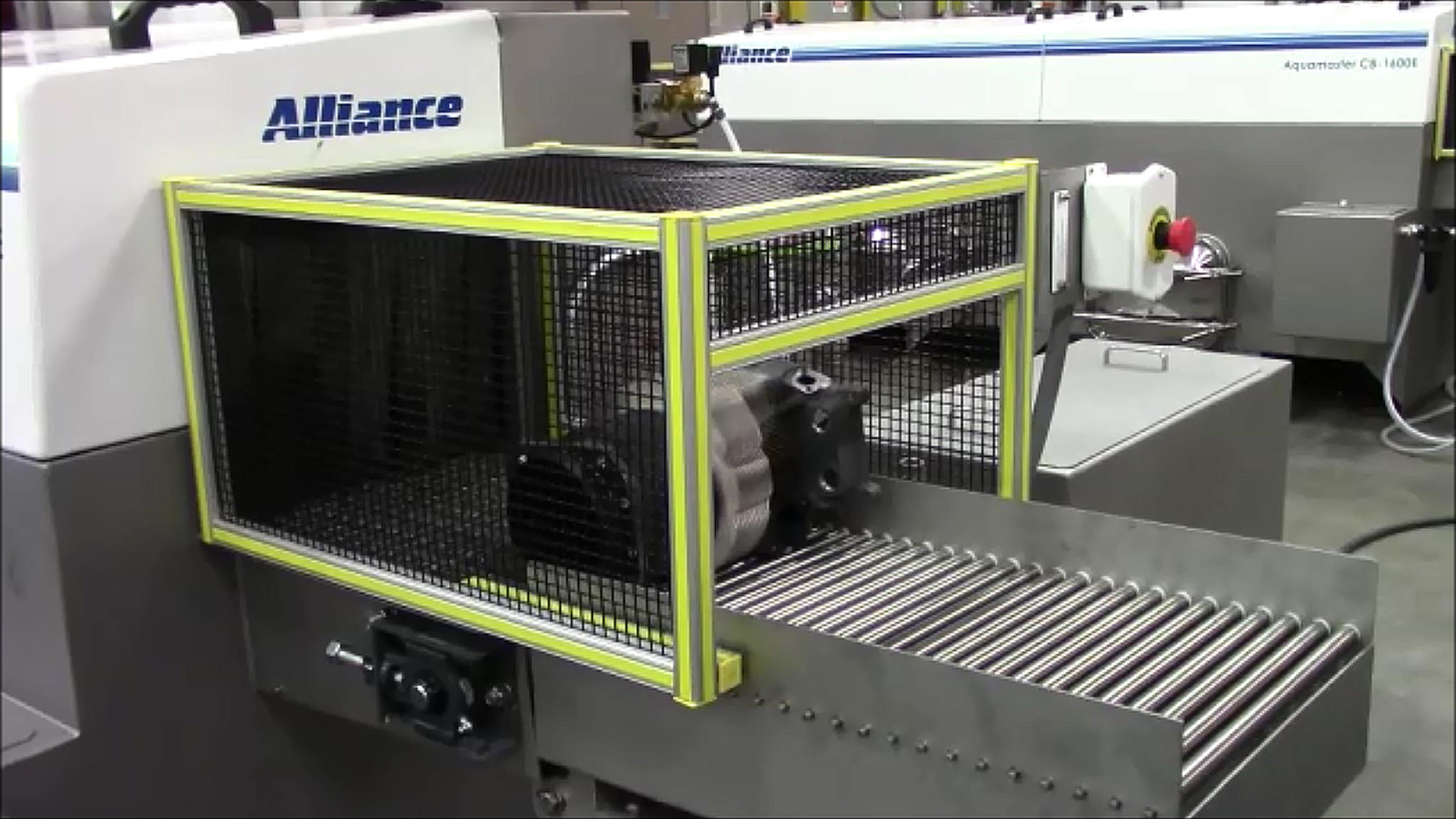
Customer Background
The customer is a leading manufacturer of aircraft engines and engine components for the general aviation industry.
Challenge
The customer needed a washing system to remove honing oils, coolant, and chips from aircraft engine cylinder assemblies. The aircraft engine cylinder assemblies needed to be visually clean, and 100% dry upon exiting the cleaning system. The production rate is approximately 600 assemblies per week.
Solution
A three-stage Aquamaster CB-1600E that includes wash, rinse, and ambient blow-off process zones was designed to meet cleaning requirements. The aircraft engine cylinder assemblies are fed through the cleaner machine with the length of the cylinder assembly running across the width of the conveyor belt.
Clip-on adjustable spray nozzles are placed on both sides of the conveyor for full wash and rinse capabilities. In order to meet the 100% dryness requirement, high-velocity adjustable air knives are located on the sides, top, and bottom of the conveyor. A stainless steel mist collector was added for removing steam generated within the washing system. Micro-filtration chambers located in both the wash and rinse zones help to filter contaminants from the solution. A stainless steel oil coalescing system was required for the removal of tramp oils and to prolong the life of the water in the wash and rinse tanks. Two segments of Alliance’s patented “Full-Access” lift-off canopy along with hinged cleanout doors were included in the design for ease of cleaning and maintenance of the aircraft engine cylinder washing machine.
A PLC control package with operator interface and machine diagnostics upgrade was incorporated to provide for quick and easy troubleshooting. This replaces the standard relay logic and selector switches. The aircraft engine cylinder assembly cleaning system was designed with overall dimensions of 13′8″ long x 5′7″ wide x 4′9″ high with a production rate of one (1) cylinder assembly every three (3) minutes.