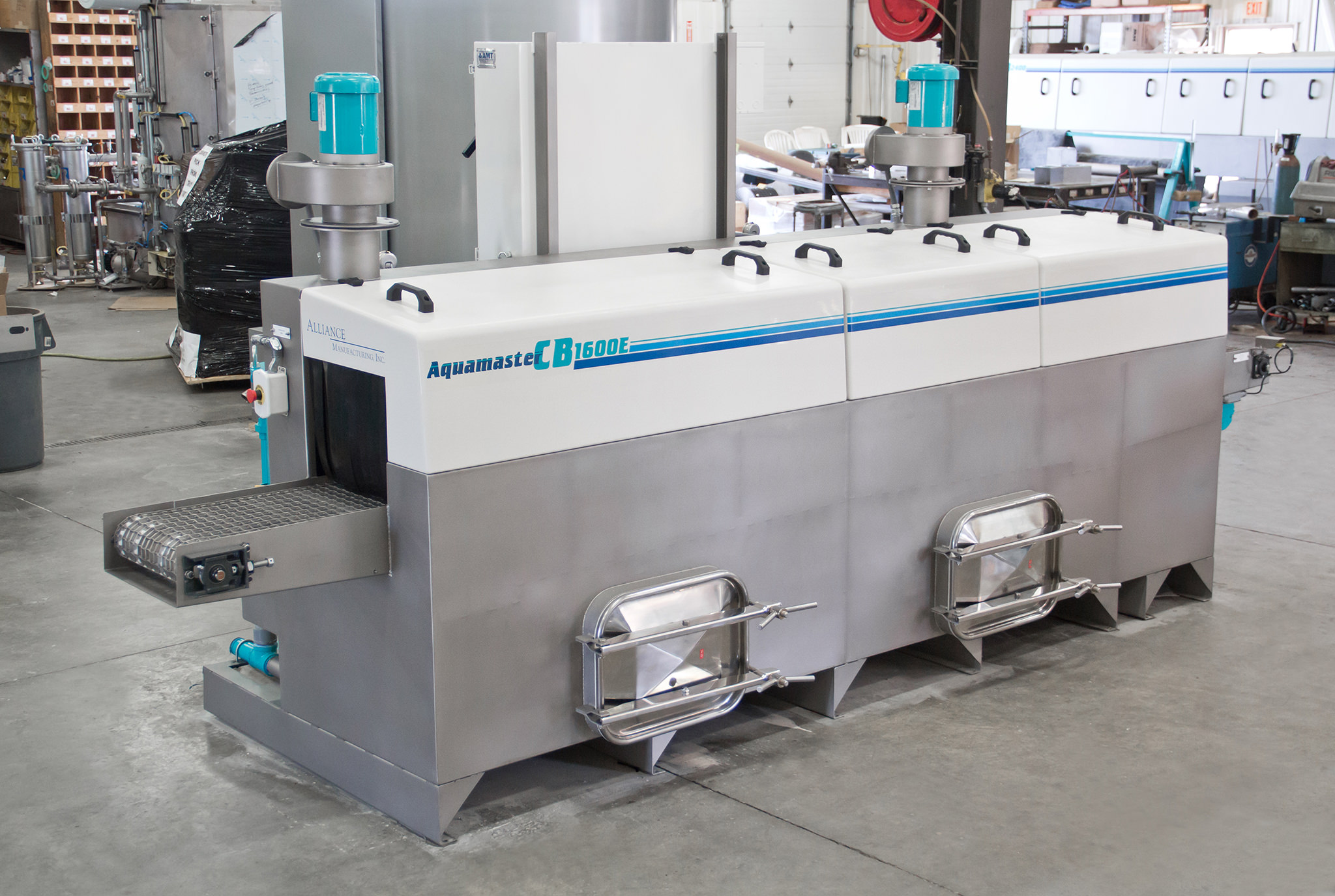
Industrial hydraulic and pneumatic systems are used in various industries to power machines and equipment. To function properly, these systems use various components, such as pumps, valves, cylinders, and hoses. However, during their use while helping to perform a manufacturing process, dirt, oils, and other contaminants can be introduced, which can negatively impact these systems’ end-use.
It should be noted that industrial hydraulic and fluid power systems are the same in that they use pressurized fluids to power machines. These fluids are generally petroleum-based oils, although other fluids, such as water, can also be used. Both systems use pumps to increase the fluid pressure, which is then transferred to a motor or other component in the system. The fluid then moves through the system, powering the components and providing the necessary force to move the machinery. In both hydraulic and fluid power systems, valves, hoses, and other components are used to control the fluid’s pressure and flow, allowing for precise control of the machine.
The maintenance of clean hydraulic and pneumatic components are crucial for optimal performance and preventing equipment failure. Contaminants can cause various issues, such as reduced efficiency, increased wear and tear, and system failure. Therefore, properly cleaning and maintaining these components is necessary to ensure they operate effectively and safely.
This article will discuss the importance of industrial hydraulic and pneumatic system parts cleaning, the components used in various industries which may need cleaning, and the various methods used to clean hydraulic and pneumatic parts. By the end of this article, you will better understand the importance of proper cleaning and maintenance in hydraulic and pneumatic systems and the benefits that come with it.
Methods of Hydraulic and Pneumatic Parts Cleaning
Several methods are used to clean hydraulic and pneumatic parts, each with advantages and disadvantages. The appropriate method will depend on the type and degree of contamination, the size and shape of the component, and the materials used in its construction.
Some common types of hydraulic and pneumatic parts cleaning include solvent cleaning, ultrasonic cleaning, dry ice blasting, and shot blasting. Read more about them below.
- Solvent Cleaning: Solvent cleaning involves immersing the component in a solvent such as mineral spirits, acetone, or alcohol to dissolve and remove contaminants. Solvent cleaning effectively removes oils, grease, and other organic compounds but may not be suitable for all materials and can be hazardous to health and the environment.
- Ultrasonic Cleaning: This method uses high-frequency sound waves to create cavitation bubbles that loosen and remove contaminants from the component’s surface. Ultrasonic cleaning removes dirt, oil, and other contaminants from small, intricate parts. This method may not be as effective in removing stubborn contaminants, especially on complex components and ultrasonic cleaning equipment can be expensive.
- Dry Ice Blasting: This method uses compressed air to blast dry ice pellets onto the component’s surface, removing contaminants by thermal shock and mechanical force. Dry ice blasting effectively removes stubborn contaminants such as carbon buildup and can be used on various materials. Dry ice blasting equipment can be much more expensive and is not effective when removing thick layers of contaminants.
- Shot Blasting – Shot blasting involves propelling abrasive particles at high speed onto parts to remove contaminants and improve the part’s surface finish. This method effectively removes metal parts’ rust, paint, and other surface coatings. Shot blasting may not be effective when removing hard-to-reach areas, particularly those with internal cavities or irregular shapes. Also softer metals and plastics are prone to surface damage with shot blasting.
Proper selection of the cleaning method depends on the type of component, the degree of contamination, and the desired level of cleanliness. It is essential to follow industry standards and best practices to ensure that parts are cleaned effectively and safely.
While these traditional methods are adequate for some applications, Alliance focuses on vacuum degreasing and aqueous cleaning as the most effective methods of hydraulic and pneumatic parts cleaning
Vacuum Degreasing
Vacuum degreasing, also known as vacuum cleaning, is a cleaning process used to remove contaminants such as oil, grease, and dirt from metal parts. This method is particularly effective for removing contaminants from complex parts, such as those with small crevices or holes, that are difficult to clean using traditional methods.
The vacuum degreasing process works by placing the metal parts into a vacuum chamber and heating them to a specific temperature, typically around 176-194°F (or 80-90°C). The chamber is then evacuated to create a vacuum, typically between 0.1 and 10 Torr, which causes the contaminants to evaporate.
The evaporated contaminants are then condensed onto a cooled surface, typically a condenser coil, where they can be removed from the system. The metal parts are left clean and dry, free of contaminants.
Vacuum degreasing has several advantages over traditional cleaning methods. First, it is a non-aqueous cleaning process, meaning it does not use water or other liquids, reducing the risk of corrosion and other damage to the metal parts. Additionally, vacuum degreasing is an environmentally friendly cleaning method, producing no waste water or harmful emissions.
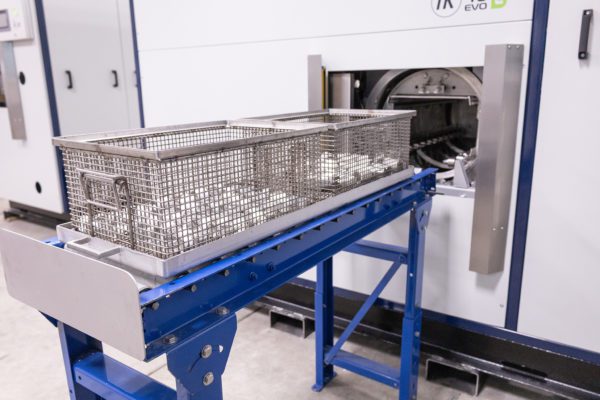
Aqueous Cleaning
Aqueous cleaning is a cleaning method that uses water-based solutions to remove contaminants from metal parts. The process involves placing the metal parts into a cleaning solution, typically a mixture of water and a detergent or surfactant, and agitating the solution to dislodge and dissolve the contaminants.
Several types of aqueous cleaning methods include spray cleaning, immersion cleaning, and ultrasonic cleaning. The solution is sprayed onto the metal parts using high-pressure nozzles in spray cleaning. In contrast, in immersion cleaning, the parts are immersed in the cleaning solution and agitated using mechanical or ultrasonic means. Ultrasonic cleaning uses high-frequency sound waves to create microscopic cavitation bubbles that help to dislodge and remove contaminants from the metal parts.
Aqueous cleaning has several advantages over other cleaning methods. First, it is a safe and environmentally friendly cleaning method, as it does not use harsh chemicals or solvents that can harm workers or the environment. Aqueous cleaning is also effective at removing a wide range of contaminants, including oils, greases, and particulates, and is compatible with various metals and alloys.
Components of Hydraulic Systems Used in Various Industries
Hydraulic systems are essential components in various industries. These systems have different components that provide efficient and reliable operation. Some of the commonly used hydraulic components in these industries include:
- Hydraulic Pumps – Hydraulic pumps generate the hydraulic pressure that powers the system. There are various types of hydraulic pumps, such as gear pumps, vane pumps, and piston pumps.
- Hydraulic Valves – Hydraulic valves control the flow of hydraulic fluid within the system. There are various hydraulic valves, such as directional, pressure, and flow control valves.
- Hydraulic Cylinders – Hydraulic cylinders create linear motion in hydraulic systems. They convert hydraulic pressure into mechanical force and are used in various applications such as lifting and pushing.
- Hydraulic Hoses – Hydraulic hoses transport hydraulic fluid between components in the system. They are flexible, durable, and designed to withstand high pressures and temperatures.
- Hydraulic Filters – Hydraulic filters remove contaminants from the hydraulic fluid and help to keep the system clean. They are crucial for preventing damage to components and ensuring proper system functioning.
Hydraulic components are used extensively in a variety of industries including construction, mining, manufacturing, and agriculture. Here are some specific examples of how hydraulic components are used in each industry:
- Construction: Hydraulic components are commonly used in heavy construction equipment such as excavators, bulldozers, and cranes. Hydraulic systems are used to power the movement of the equipment, lift and lower heavy loads, and control the movement of the equipment arms and attachments. For example, hydraulic cylinders are used to power the movement of the boom and bucket on an excavator.
- Mining: Hydraulic systems are used in mining equipment such as dump trucks, loaders, and drilling machines. These systems are used to power the movement of the equipment, lift and lower heavy loads, and control the movement of the drilling bits and other tools. For example, hydraulic systems are used to power the hydraulic shovels that load the ore into trucks in an open pit mine.
- Manufacturing: Industrial hydraulic systems are used in manufacturing equipment such as presses, stamping machines, and injection molding machines. These systems are used to power the movement of the equipment, apply pressure to the materials being processed, and control the speed and force of the equipment. For example, hydraulic systems are used to power the presses that shape metal parts in a factory.
- Agriculture: Hydraulic systems are used in agricultural machinery such as tractors, harvesters, and plows. These systems are used to power the movement of the equipment, lift and lower heavy loads, and control the movement of the equipment arms and attachments. For example, hydraulic systems are used to power the arms and attachments on a combine harvester.
Pneumatic Components Used in Various Industries
Pneumatic systems are essential components in various industries. These systems have different components that provide efficient and reliable operation. Some of the commonly used pneumatic components in these industries include:
- Pneumatic Compressors – Pneumatic compressors generate compressed air that powers the system. They are available in various sizes and configurations and can be powered by electricity or gasoline.
- Pneumatic Valves – Pneumatic valves control the flow of compressed air within the system. They are available in various types, such as directional, pressure, and flow control valves.
- Pneumatic Cylinders – Pneumatic cylinders create linear motion in pneumatic systems. They convert compressed air into mechanical force and are used in various applications such as lifting and pushing.
- Pneumatic Hoses and Fittings – Pneumatic hoses and fittings transport compressed air between components in the system. They are flexible, durable, and designed to withstand high pressures and temperatures.
- Pneumatic Filters and Regulators – Pneumatic filters and regulators remove contaminants from the compressed air and help regulate the system’s pressure. They are crucial for preventing damage to components and ensuring proper system functioning.
Pneumatic components are used extensively in a variety of industries including manufacturing, food processing, and automotive. Here are some specific examples of how pneumatic components are used in each industry:
- Manufacturing: Pneumatic systems are commonly used in manufacturing applications such as assembly lines, material handling, and packaging equipment. Pneumatic cylinders are used to power the movement of equipment and tools, and pneumatic valves are used to control the flow of air to the equipment. For example, pneumatic systems are used to power the automated assembly line machines that put together small parts in a factory.
- Food Processing: Pneumatic systems are used extensively in the food processing industry, especially for packaging and handling food products. Pneumatic actuators are commonly used to control the flow of fluids and gasses in the processing equipment, and pneumatic valves are used to control the flow of air and other gasses in the packaging equipment. For example, pneumatic systems are used to power the machines that fill and seal bags of snacks in a food processing plant.
- Automotive: Pneumatic systems are used in various applications in the automotive industry, such as braking systems, suspension systems, and engine control systems. Pneumatic cylinders are used to power the movement of the equipment, and pneumatic valves are used to control the flow of air and other gasses in the system. For example, pneumatic systems are used to power the air suspension systems in luxury cars.
Hydraulic and pneumatic parts cleaning is essential for many industries to ensure the reliability and safety of the equipment. Over time these components can become contaminated with dirt, dust, and other particles, which can cause the equipment to malfunction or fail. This can result in downtime, lost productivity, and costly repairs.
Effects of Dirt, Oils, and Other Contaminants in Hydraulic and Pneumatic Components
Dirt, oils, and other contaminants introduced during the manufacturing or use of hydraulic and pneumatic components can negatively impact the system’s performance and lifespan. Here are some of the effects of contaminants in hydraulic and pneumatic components:
- Reduced Efficiency – Contaminants in the hydraulic or pneumatic fluid can cause restrictions in the flow, leading to a decrease in the efficiency of the system. This can result in the system’s slower or less effective operation, reducing productivity and potentially causing safety issues.
- Increased Wear and Tear – Contaminants can cause damage to the components of the system, leading to increased wear and tear. This can result in more frequent maintenance or replacement of components, increasing downtime and costs.
- Malfunctioning Components – Contaminants can cause components such as valves and cylinders, leading to system failure and potentially causing safety hazards.
- Corrosion – Contaminants such as moisture can cause corrosion of the components, reducing their lifespan and potentially causing leaks or system failure.
Importance of Starting with Clean Components
Starting with perfectly clean components is crucial in hydraulic and pneumatic systems because any dirt, oils, or other contaminants left on the components can negatively impact the performance and longevity of the system. For example, contaminants introduced during the manufacturing or assembly process of hydraulic and pneumatic components can cause several issues, including reduced efficiency, premature wear and tear, and system failure. Meanwhile, dirt and debris in hydraulic oil can cause blockages in the system, leading to reduced fluid flow and pressure. Similarly, oils and greases on pneumatic components can attract and trap dirt and dust, causing valve sticking and reduced cylinder performance.
Moreover, contaminants can lead to increased maintenance costs and downtime, as the hydraulic and pneumatic system may require frequent repairs or component replacements. Therefore, starting with perfectly clean components is critical to ensure optimal system performance and longevity.
Proper cleaning and maintenance of hydraulic and pneumatic components are also essential in preventing system contamination. Therefore, following manufacturer recommendations for cleaning and maintenance is crucial as using the appropriate cleaning methods and solutions for the components and contaminants involved. Starting with perfectly clean components and maintaining a clean system can significantly reduce the risk of contamination and associated issues, leading to improved system reliability and cost savings in the long run.
Conclusion
Hydraulic and pneumatic parts cleaning is critical for ensuring the optimal performance and lifespan of fluid power systems. Contaminants such as dirt, debris, and moisture can cause damage to components, leading to reduced efficiency, increased wear and tear, and potentially causing safety hazards.
Proper cleaning and maintenance of hydraulic and pneumatic components can help prevent contamination and ensure optimal system performance. This includes using appropriate cleaning techniques and equipment, following proper maintenance procedures, and maintaining a clean environment.
While there are challenges associated with hydraulic and pneumatic parts cleaning, the benefits, including increased efficiency, improved lifespan, reduced costs, and enhanced safety, make it a necessary investment for industries that rely on fluid power systems.
In conclusion, hydraulic and pneumatic parts cleaning is an essential process that should be performed regularly to ensure the optimal performance and lifespan of fluid power systems. By choosing Alliance’s parts cleaning machinery, you can get your hydraulic and pneumatic components clean for the end-user.